معرفی مواد سازنده آهنربا بیان میکند که چند نوع آهنربا داریم و کاربرد هر یک از انواع آهنربا و مواد مغناطیسی در کجاست. آهنرباها علاوه بر مواد اولیه بر اساس روشهای ساخت نیز به دستههای مختلفی تقسیم میشوند. در ادامه به بررسی مفهوم آهنربا و معرفی برخی از انواع اصلی آهنرباها و روشهای ساخت آنها میپردازیم.
آهنربا چیست؟
آهنربا جسمی است که یک میدان مغناطیسی ساکن را با خود حمل می کند. حتی ذرات منفرد مانند الکترونهای در حال چرخش نیز، میدانهای مغناطیسی در اطراف خود دارند، بنابراین میتوانیم الکترونها را نیز «آهنربا» بنامیم. آهنرباهای دائمی در واقع آن دسته از موادی هستند که در آنها الکترون ها بیشتر در یک جهت می چرخند. بیشتر الکترونهای موجود در اکثر مواد با الکترونهای دیگری که در جهت مخالف میچرخند جفت میشوند، اما برخی از مواد مانند آهن دارای تعداد زیادی الکترون جفت نشده هستند. اینها وقتی با یکدیگر برهمکنش می کنند می توانند مغناطیس خالص ایجاد کنند به طوری که هنگام چرخش در یک جهت انرژی کمتری داشته باشند. جاذبه ای که آهنربا ایجاد می کند “میدان مغناطیسی” نامیده می شود در واقع آهنربا ماده یا جسمی است که میدان مغناطیسی نامرئی تولید می کند که می تواند به سمت مواد فرومغناطیسی جذب شود.
آهنربای طبیعی:
مگنتیت (سنگ آهنربا): نوعی سنگ معدنی که به طور طبیعی خاصیت مغناطیسی دارد. این نوع آهنرباها معمولاً در طبیعت یافت میشوند و اولین آهنرباهای شناختهشده توسط بشر بودهاند.
آهنرباهای مصنوعی:
دائمی و الکتریکی
1. آهنرباهای الکتریکی
آهنرباهای الکتریکی با استفاده از جریان الکتریکی تولید میشوند و تنها زمانی که جریان الکتریکی در سیم پیچ عبور میکند، خاصیت مغناطیسی دارند. انواع آهنرباهای الکتریکی شامل:
- آهنربای سیمپیچی شده: در این نوع آهنربا، سیم مسی به دور یک هسته آهنی پیچیده میشود و با عبور جریان الکتریکی از سیم، هسته مغناطیسی میشود.
- آهنربای الکترودینامیکی: این نوع آهنربا در بلندگوها و میکروفونها استفاده میشود و با استفاده از جریان الکتریکی خاصیت مغناطیسی پیدا میکند.
فرآیند تولید آهنربای الکتریکی موقت
برای ساخت آهنربای موقت یا آهنربای سیم پیچی شده، یک سری لوازم ساده مورد نیاز است از جمله: یک تکه سیم مسی، یک منبع تغذیه (مانند باتری 1.5 ولت یا بیشتر)، یک میخ فلزی یا یک قطعه آهن و نوار چسب (در صورت نیاز). طی مراحل زیر آهنربای الکتریکی حاصل میشود:
ابتدا باید سیم مسی چندین بار (حدود 20 تا 50 بار) دور میخ فلزی یا قطعه آهن پیچیده شود. پیچیدن سیم باید به طور منظم و نزدیک به هم باشد. دو سر سیم باید بیرون بماند تا به باتری متصل شود. یکی از سرهای سیم به قطب مثبت و دیگری باید به قطب منفی باتری وصل شود. برای این کار میتوان از نوار چسب استفاده کرد تا اتصال محکمی برقرار شود.
با جریان یافتن برق در سیم پیچیده شده به دور میخ، یک میدان مغناطیسی ایجاد میشود و میخ فلزی به یک آهنربای موقت تبدیل میشود. این آهنربا میتواند اجسام فلزی کوچک را جذب کند. با جدا کردن سیمها از باتری، میدان مغناطیسی از بین میرود و میخ خاصیت آهنربایی خود را از دست میدهد.
**توجه:** برای ایمنی، مراقب باشید که سیم بیش از حد گرم نشود و باتریها بیش از حد داغ نشوند.
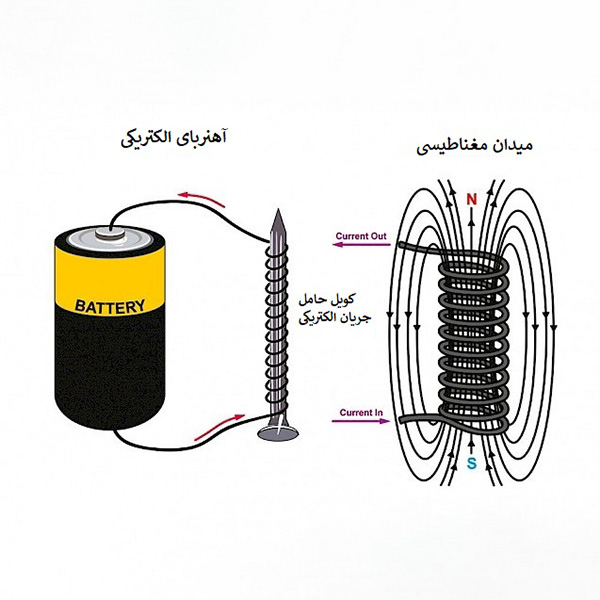
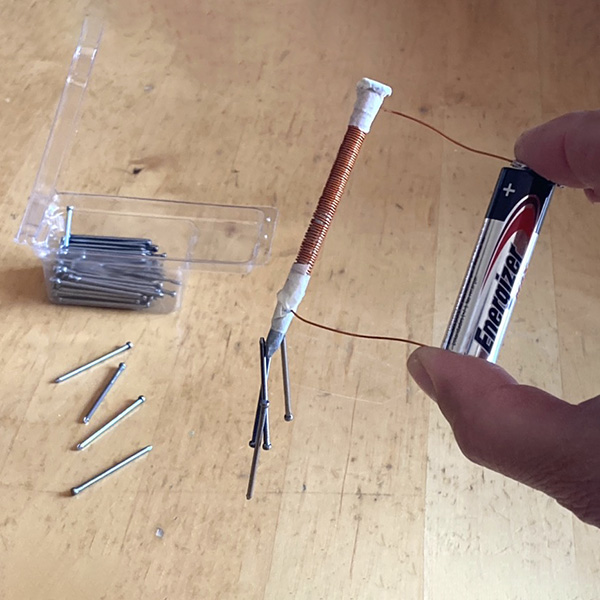
2. آهنرباهای دائمی
این نوع آهنرباها به صورت دائمی خاصیت مغناطیسی دارند و شامل مواد زیر میشوند:
- آهنربای نئودیمیوم (NdFeB): این آهنرباها از نئودیمیوم، آهن و بور ساخته میشوند و بسیار قوی هستند. روش ساخت آنها شامل ذوب و ریختهگری، آسیاب پودر و پرس گرم یا سرد است.
- آهنربای ساماریوم-کبالت (SmCo): این آهنرباها از ساماریوم و کبالت ساخته میشوند و مقاومت بالایی در برابر حرارت دارند. روش ساخت شامل ذوب و ریختهگری و سپس آسیاب و پرس است.
- آهنربای آلنیکو (Alnico): این آهنرباها از آلومینیوم، نیکل، کبالت و آهن ساخته میشوند و مقاومت خوبی در برابر حرارت دارند. روش ساخت شامل ذوب و ریختهگری و سپس عملیات حرارتی است.
- آهنربای سرامیکی (فریت): این آهنرباها از اکسید آهن و باریم یا استرانسیوم ساخته میشوند و به دلیل هزینه کم و مقاومت در برابر خوردگی معروف هستند. روش ساخت شامل مخلوط کردن مواد اولیه، آسیاب کردن، شکلدهی و پخت در دمای بالا است.
روشهای ساخت آهنربا
فرایند های ساخت آهنربا به مواد اولیه و نوع آهن ربا بستگی دارد. فرآیندهای مختلفی برای ساخت آهنربا وجود دارد، یکی از متداول ترین روشها متالورژی پودر نام دارد. در این فرآیند، یک ترکیب مناسب به پودر ریز تبدیل شده، فشرده میشود و حرارت داده میشود تا از طریق «سینترینگ فاز مایع» چگالش شود. بنابراین، این آهنرباها اغلب آهنرباهای متخلخل نامیده می شوند. آهنرباهای فریت، ساماریوم کبالت (SmCo) و آهنرباهای نئودیمیم-آهن-بور (نئو) همگی با این روش ساخته می شوند. برخلاف فریت که یک ماده سرامیکی است، همه آهنرباهای خاکی کمیاب آلیاژهای فلزی هستند. در مورد مگنت های SMCO و NEO مواد خام مناسب تحت خلاء یا گاز بی اثر در کوره ذوب القایی، ذوب می شوند. آلیاژ مذاب یا در قالب و بر روی یک صفحه خنک کننده ریخته می شود( یک نوار ریخته گری یا قالب ریخته گری نازک). این “نوارها یا تکه های” فلزی زینتر شده خرد و پودر می شوند تا پودر ریز به قطر 3 تا 7 میکرون بدست آید. این پودر بسیار ریز از نظر شیمیایی واکنش پذیر است و می تواند به طور خود به خود در هوا مشتعل شود، بنابراین باید از قرار گرفتن در معرض اکسیژن محافظت شود و در نهایت از روشهای مختلفی برای فشردهسازی پودر حاصل استفاده میکنند (پرس محوری یا عرضی و پرس ایزواستاتیک).
اگرچه می توان از این آلیاژها اشکال آهنربایی پیچیده تولید کرد، اما این مواد برای اشکال ساده تر مناسب هستند. سوراخ ها، پخ های بزرگ یا شکاف ها هزینه بیشتری برای تولید دارند. نگه داشتن تلورانس ها بر روی اشکال پیچیده تر که احتمالاً منجر به تغییرات میدان شار و فشار فیزیکی بالقوه قطعه در یک مجموعه می شود، دشوارتر است.
آهنرباهای ماشینکاری شده دارای لبه های تیز خواهند بود که مستعد بریدگی هستند. پوشش اطراف لبه تیز نیز مشکل ساز است. متداولترین روش برای کاهش تیزی، سنگزنی ارتعاشی است که اغلب غلتش ارتعاشی نامیده میشود و در محیط ساینده انجام میشود.
آهنرباهای نئو که مستعد زنگ زدگی یا واکنش شیمیایی هستند، تقریباً همیشه پوشش داده می شوند. کبالت ساماریوم به طور طبیعی نسبت به نئودیمیوم در برابر خوردگی مقاومتر است، اما در مواردی از پوشش نیز استفاده میکندد. رایج ترین پوشش های محافظ شامل اپوکسی خشک پاشیده شده، پوشش الکترونیکی (اپوکسی)، نیکل الکترولیتی، آلومینیوم IVD (پوشش دهی بخار یون آلومینیوم) و ترکیبی از این پوشش ها می باشد. آهنرباها را می توان با پوشش های تبدیلی مانند روی، آهن یا منگنز فسفات ها و کرومات ها نیز پوشاند. پوششهای تبدیلی عموماً برای محافظت موقت کافی هستند و میتوانند یک لایه زیرین برای پوشش اپوکسی یا یک لایه روی برای افزایش حفاظت در برابر IVD آلومینیوم تشکیل دهند.
در کل برخی از روشهای معمول عبارتند از:
- ذوب و ریختهگری: این روش برای ساخت آهنرباهای آلنیکو و برخی آهنرباهای نئودیمیوم استفاده میشود.
- آسیاب کردن و پرس: این روش برای ساخت آهنرباهای فریت و نئودیمیوم استفاده میشود.
- شکلدهی و پخت: این روش برای ساخت آهنرباهای سرامیکی (فریت) استفاده میشود.
- پرس گرم یا سرد، پرس محوری، پرس ایزواستاتیک: این روش برای آهنرباهای نئودیمیوم و ساماریوم-کبالت استفاده میشود.
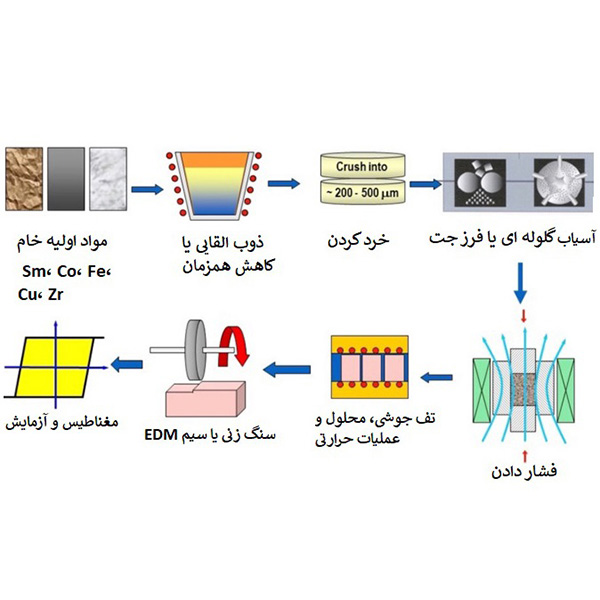
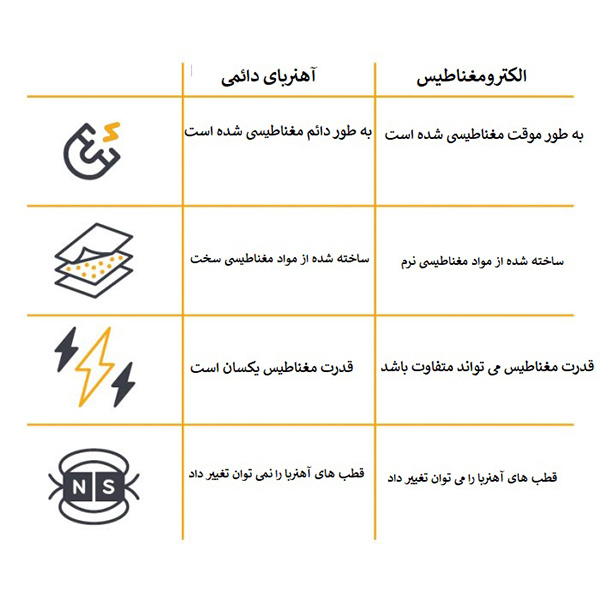
معرفی آهنربای فریت سرامیکی تولید شده به روش فرآیند متالورژی پودر
آهنرباهای فریت می توانند همسانگرد یا ناهمسانگرد باشند. آهنرباهای فریت ایزوتروپیک می توانند در هر جهتی مغناطیسی شوند اما دارای خواص مغناطیسی ضعیف تری هستند. آهنرباهای فریت ناهمسانگرد دارای جهت مغناطیسی ترجیحی در ساختار هستند و قوی ترین خواص مغناطیسی را در امتداد آن جهت دارند (قوی تر از آهنرباهای فریت همسانگرد هستند).
دو نوع شیمیایی آهنربای فریت وجود دارد:
- فریت استرانسیوم با دو نماد شیمیایی SrFe12O19 یا SrO.6Fe2O3.
- فریت باریم با دو نماد شیمیایی BaFe12O19 یا BaO.6Fe2O3
آهنرباهای فریت (مگنت های سرامیکی) با کلسینه کردن (در دمای بین 1000 تا 1350 درجه سانتیگراد) مخلوطی از اکسید آهن (Fe2O3) و کربنات استرانسیم (SrCO3) یا کربنات باریم (BaCO3) برای تشکیل اکسید فلزی تولید می شوند. در برخی گریدها، مواد شیمیایی دیگری مانند کبالت (Co) و لانتانیم (La) برای بهبود عملکرد مغناطیسی اضافه میشوند. سپس این اکسید فلزی تا رسیدن به اندازه ذرات کوچک آسیاب می شود (اندازه کمتر از یک میلی متر؛ معمولاً چند میکرون). سپس این فرآیند بسته به نوع آهنربای مورد نیاز، دو گزینه تولید اصلی دارد.
اولین مورد فشار دادن پودر ریز خشک در قالبی است که منجر به ایجاد آهنربای همسانگرد می شود که تحمل ابعادی بهتری دارد (اغلب نیازی به ماشینکاری بیشتر تا اندازه نهایی ندارد). ساختار کریستالی هگزاگونال است و این امکان را فراهم میکند که آهنربا در هر جهتی پس از آن مغناطیسی شود. در این روش ممکن است یک میدان مغناطیسی خارجی برای تولید آهنرباهای ناهمسانگرد نیاز باشد.
روش دوم شامل مخلوط کردن پودر ریز با آب برای تولید دوغاب است سپس در حضور یک میدان مغناطیسی خارجی اعمال شده در قالب فشرده می شود. میدان مغناطیسی خارجی اعمالی به ساختار کریستالی، میتواند عملکرد مغناطیسی آهنربا را بهبود بخشد. آب موجود در دوغاب مانند یک روان کننده عمل می کند و منجر به یک آهنربای فریت ناهمسانگرد با خواص مغناطیسی قویتر میشود، اما احتمالاً برای رسیدن به ابعاد نهایی مراحل ماشینکاری اضافی نیاز دارد. گاهی اوقات یک اکستروژن مرطوب به جای پرس قالبی مرطوب انجام می شود. سپس آهنربا پس از تف جوشی به اندازه مورد نیاز بریده می شود.
در ادامه آهنرباهای فشرده (در دمایی بین 1100 تا 1300 درجه سانتیگراد) تف جوشی می شوند تا ذرات با هم ذوب شوند. ماشینکاری نهایی با استفاده از ابزارهای برش الماس انجام می شود. غالباً سطوح مربوط به قطب های مغناطیسی تا زبری مورد نیاز ماشینکاری می شوند و سایر سطوح در حالت زینتر شده باقی می مانند. سپس آهنربا شسته و خشک می شود قبل از اینکه تا حد اشباع مغناطیسی شود، بازرسی و برای ارسال به مشتری بسته بندی می شود.
آهنرباهای فریت ساخته شده با پرس مرطوب دارای خواص مغناطیسی بهتری هستند اما به احتمال زیاد تحمل ابعادی بیشتری دارند. آهنربای فریت سخت ناهمسانگرد خشک، دارای خواص مغناطیسی کمتری نسبت به فریت سخت ناهمسانگرد مرطوب است.
فرآیندهای ساده شده:
- SrCO3 + Fe2O3 = SrOFe2O3 + CO2
- SrOFe2O3 + 5Fe2O3 = SrO.6(Fe2O3)
- BaCO3 + Fe2O3 = BaOFe2O3 + CO2
- BaOFe2O3 + 5Fe2O3 = BaO.6(Fe2O3)
آیا میتوان از پودر مگنتیت به عنوان آهنربا استفاده کرد؟
پودر مگنتیت (Fe₃O₄) خود به تنهایی خاصیت مغناطیسی دارد، اما به دلیل پراکندگی ذرات و نبود ساختار منسجم، نمیتواند به طور مؤثر مانند یک آهنربای دائمی عمل کند. برای استفاده از پودر مگنتیت به عنوان یک آهنربا، باید آن را به شکل فشرده و با استفاده از یک چسب مغناطیسی به کار برد. این نوع ساختارها معمولاً به اندازه آهنرباهای دائمی قوی نیستند و ممکن است به مرور زمان خاصیت مغناطیسی خود را از دست بدهند.
مگنتیت آهنربای قوی تری است یا فریت؟
مگنتیت (Fe₃O₄) یک ماده مغناطیسی طبیعی است که به طور طبیعی خاصیت مغناطیسی دارد، اما به عنوان یک آهنربا، قدرت مغناطیسی آن نسبت به آهنرباهای مصنوعی مانند فریت کمتر است. مگنتیت بیشتر به عنوان ماده اولیه برای تولید آهنرباها و دیگر مواد مغناطیسی استفاده میشود. فریتها آهنرباهای سرامیکی هستند که از ترکیب اکسید آهن با فلزات دیگر مانند باریم یا استرانسیوم ساخته میشوند.
فریتها به عنوان آهنرباهای دائمی استفاده میشوند و در مقایسه با مگنتیت، قدرت مغناطیسی بیشتری دارند. همچنین، فریتها مقاومت بالاتری در برابر دما دارند و در برابر زنگزدگی و خوردگی مقاومتر هستند.
خاصیت آهنربایی پودر مگنتیت بیشتر است یا پودر آهن احیا شده؟
خاصیت مغناطیسی پودر مگنتیت و پودر آهن احیا شده به ترکیب شیمیایی و ساختار کریستالی آنها بستگی دارد. مگنتیت یک اکسید آهن است که دارای ترکیب شیمیایی Fe₃O₄ میباشد. به طور طبیعی خاصیت مغناطیسی دارد و یک ماده فرومغناطیس است اما نسبت به برخی مواد مغناطیسی مصنوعی ضعیفتر است.
پودر آهن احیا شده معمولاً از آهن خالص (Fe) تشکیل شده است. این ماده از طریق فرایند احیا از اکسیدهای آهن تولید میشود. آهن خالص نیز یک ماده فرومغناطیس است و خاصیت مغناطیسی بالایی دارد. آهن خالص به طور کلی خاصیت مغناطیسی قویتری نسبت به مگنتیت دارد. وقتی پودر آهن تحت تأثیر یک میدان مغناطیسی قرار میگیرد، میتواند خاصیت مغناطیسی بیشتری به خود بگیرد.
پودر آهن احیا شده برای ساخت آهنربا استفاده میشود؟
پودر آهن احیا شده به طور مستقیم برای ساخت آهنرباهای دائمی مورد استفاده قرار نمیگیرد، اما به دلیل خواص مغناطیسی آن، در برخی فرآیندها و کاربردها مورد استفاده قرار میگیرد. پودر آهن احیا شده میتواند در ساخت آهنرباهای نرم که به راحتی مغناطیسی و غیرمغناطیسی میشوند (مانند هستههای مغناطیسی در ترانسفورماتورها) استفاده شود. این نوع آهنرباها پس از حذف میدان مغناطیسی، خاصیت مغناطیسی خود را از دست میدهند. برای ساخت **آهنرباهای دائمی** که خاصیت مغناطیسی خود را برای مدت طولانی حفظ میکنند، از مواد مغناطیسی با خواص مغناطیسی قویتر و پایدارتر مانند نئودیمیوم، ساماریوم-کبالت، یا فریت استفاده میشود.
https://www.arnoldmagnetics.com/resources/magnet-manufacturing-process/
https://www.stanfordmagnets.com/manufacturing-methods-of-permanent-magnets.html
https://e-magnetsuk.com/ferrite-magnets/how-ferrite-magnets-are-made/