کاربرد پودر آهن
کشف فلز آهن را می توان نقطه عطفی در تاریخ تکاملی بشر نامید. ما از این فلز سود زیادی بردهایم و بیشتر پیشرفتها را میتوان به آهن و فولاد نسبت داد. در حالی که برای مردم عادی، آهن بیشتر یک مصالح ساختمانی است، اما کاربردهای قابل توجهی نیز از آن در صنایع مختلف وجود دارد. بسیاری از این کاربردها از پودر آهنی که به صورت میکرو تا نانو دانه های فلز آهن خالص ارائه می شود، ایجاد می شود. با توجه به خواص فیزیکی ویژه ای که از چنین ذرات آهن به دست می آید، این ذرات به انتخابی بی چون و چرا در کاربردهای مختلف شیمیایی تبدیل شده اند.
سپس این کاربردها توسط صنایع مختلف اعم از متالورژی پودر، چاپ و بسته بندی مواد غذایی گرفته تا جوشکاری، الکترود سازی، سگمنت برشی، تولید فشفشه، رنگ و تصفیه مورد استفاده قرار می گیرند. تولید کنندگان پودر فلز مطابق با خواسته های سفارشی مشتریان خود در بخش های مختلف صنعتی به این نیازها پاسخ می دهند. در اینجا کاربردهای خاص پودر آهن برای صنایع شیمیایی آورده شده است.
1-ساخت سیستم های تصفیه آب
پودر آهن در ساخت نمک های آهنی جهت تصفیه آب استفاده می شود. برای این منظور از کلرید آهن و اکسیدهای آهن مانند مگنتیت استفاده می شود که از پودر آهن به دست می آید.
2-برش پودری فولاد
پودر آهن هنگامی که در مشعل اکسی استیلن استفاده می شود، دمای شعله را افزایش می دهد و در نتیجه راندمان برش فولاد را افزایش می دهد. علاوه بر این، سرباره تولید شده نیز رقیق می شود که در صورت عدم وجود ذرات آهن، مقاومت حرارتی ایجاد می کند.
3-بسته بندی غذا
کیسه های پودر آهن به دلیل خاصیت جذب اکسیژن فلز در بسته های مواد غذایی استفاده می شود. تولید کنندگان پودر فلز پودر آهن بسیار ریز و با خلوص بالا را ارائه می دهند که توسط صنایع فرآوری مواد غذایی استفاده می شود. پودر آهن همچنین در صنایع غنی سازی مواد غذایی و داروسازی برای تولید مکمل ها استفاده می شود.
4-برای افزایش رسانایی
آهن رسانای خوبی برای گرما است. از این رو اغلب در محصولات پلیمری با اهمیت صنعتی استفاده می شود. با تقویت پلیمر با مقدار مناسب پودر آهن، هدایت حرارتی متناسب با کاربرد خاص افزایش می یابد.
5-تولید رنگ های مغناطیسی
در ساخت رنگ های مغناطیسی و تخته های مغناطیسی از پودرهای آهن به عنوان پوشش روی سطح استفاده می شود. برای ساختن چنین رنگ های مغناطیسی از پودر آهن بسیار ریز استفاده می شود.
6-کاتالیزورهای صنعتی
تولید کنندگان پودر آهن برای صنایع شیمیایی، پودرهای آهن با عیار بالا و خلوص 100% را در اندازه دانه های مختلف عرضه می کنند تا با کاربردهای کاتالیزوری در واکنش های صنعتی مطابقت داشته باشند.
7-حذف ناخالصی گوگرد از سوخت های گازدار
پودر آهن برای تصفیه سوخت های گازی شده به ویژه حذف گوگردی که به راحتی از طریق حضور آهن اکسید می شود استفاده می شود.
8-افزودن به پلیمرها در قطعات قالب گیری تزریقی و اکسترود شده
اجزای قالب گیری و اکسترود شده با انعطاف پذیری بالا در پلیمر با تزریق پودر آهن به عنوان پرکننده با توزیع یکنواخت ساخته می شوند. وجود پودر آهن باعث می شود که این قطعه برای کاربردهای مختلف بسیار سفت و محکم باشد. به این ترتیب ویژگی های دوگانه پلیمر و آهن به دست می آید.
روشهای تولید پودر آهن
در حال حاضر دو روش تولید اساساً متفاوت وجود دارد که مجموعاً بیش از 90 درصد از تولید جهانی پودر آهن و فولاد را تشکیل می دهند. فرآیند آهن اسفنجی هوگاناس Höganäs و فرآیند اتمیزه کردن آب. تولید آهن اسفنجی به روش فرایند کوره تونلی برای اولین بار در سوئد و در سال 1911 میلادی تحت عنوان روش هوگاناس توسعه یافت. از جهت انواع به پودر آهن احیا شده، پودر اتمیزه و پودر آهن الکترولیتی تقسیم میشود.
فرآیند اول بر اساس احیای سنگ آهن است و یک آهن اسفنجی بسیار متخلخل تولید می کند که متعاقباً به پودر تبدیل می شود. فرآیند دوم بر اساس اتمیزه کردن جریانی از آهن مایع (یا فولاد) با استفاده از یک جت آب تحت فشار است. در ادامه هر دو فرآیند به تفصیل توضیح داده خواهد شد.
در ساخت قطعات زینتر شده، همیشه از پودرهای آهن به صورت مخلوط با مقدار کمی روان کننده به صورت پودر استفاده می شود تا اصطکاک در ابزار فشرده سازی به حداقل برسد. در بسیاری از موارد، پودر آهن با عناصر آلیاژی به صورت پودر مانند گرافیت، مس، نیکل، مولیبدن و غیره (به منظور دستیابی به خواص استحکام بیشتر) مخلوط می شوند. از آنجایی که ترکیبات پودری هنگام حمل و نقل و جابجایی تمایل به جدا شدن دارند، Höganäs AB فرآیندهای اختلاط ویژه ای را ایجاد کرده است که در آن افزودنی های آلیاژی به طور دائم به ذرات پودر آهن متصل می شوند. این فرآیندها با نامهای Distaloy و Starmix شناخته شدهاند .
فرآیند آهن اسفنجی هوگاناس
فرآیند آهن اسفنجی هوگاناس، اساساً یک فرآیند شیمیایی است که در آن سنگ آهن ریز تقسیم شده با خرده کک احیا میشود و تودهای اسفنجی از آهن فلزی جامد به دست میآید که به راحتی میتوان آن را به پودر آهن تبدیل کرد. سنگ آهن مورد استفاده در Höganäs یک تکه مگنتیت (پودری Fe3O4) است که از استخراج انتخابی از معادن شمال سوئد و نروژ به دست می آید. این تکه مگنتیت که ذاتاً حاوی محتوای بسیار کم گوگرد و فسفر است، پوشانده و تغلیظ شده سپس در حالت بسیار خالص به هوگاناس تحویل داده می شود.
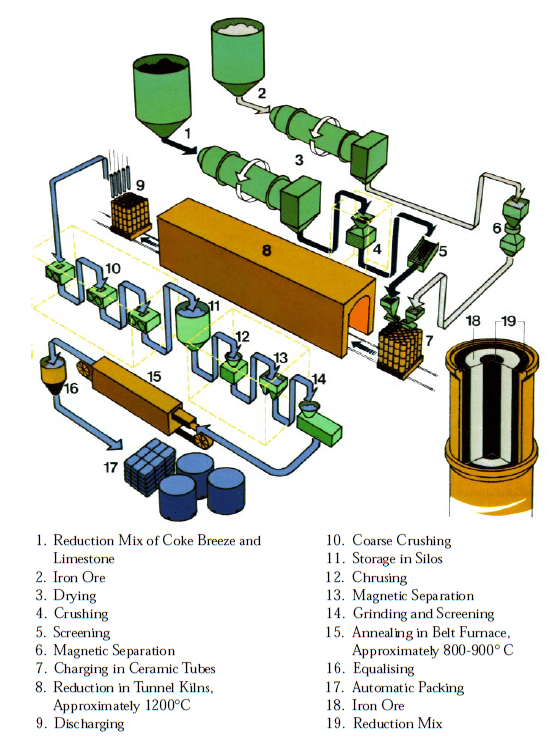
این فرآیند با دو ماده خام آغاز می شود: یک “مخلوط احیا” متشکل از خرده کک مخلوط شده با سنگ آهک زمینی (1) و یک تکه مگنتیت از پیش فرآوری شده (2). مگنتیت و مخلوط احیا به طور جداگانه در دو کوره دوار خشک می شوند (3). مخلوط احیای خشک شده که کمی آگلومره شده خرد شده (4) و غربال می شود (5) و تکه مگنتیت خشک شده از یک جداکننده مغناطیسی (6) عبور می کند. سپس، هر دو ماده با استفاده از یک دستگاه شارژ خودکار در مخازن سرامیکی لوله مانند شارژ می شوند، همانطور که در بخش (7)، (18)، (19) شکل نشان داده شده است. این قفسه ها دارای شناسه 40 سانتی متری، طول 2 متر و چهار بخش لوله کاربید سیلیکون هستند که روی هم قرار گرفته اند.
این قابها، هر کدام 25 عدد، بر روی واگنهای محدود به ریل که با لایهای ضخیم از آجرهای نسوز پوشانده شدهاند، ایستادهاند. این خودروها یا واگن ها به آرامی از میان یک کوره تونلی به طول تقریبی 260 متر (8) حرکت می کنند که در داخل آن کوره ها به تدریج تا حداکثر دمای حدوداً 1200 درجه سانتی گراد گرم می شوند. با افزایش دمای داخل قفسه ها، خرده کک شروع به سوختن میکنند و CO تشکیل می شود که به نوبه خود شروع به احیا یا تبدیل مگنتیت به آهن فلزی می کند در حالی که خود به CO2 اکسید می شود.
CO2 تولید شده با خرده کک باقیمانده واکنش نشان می دهد و CO جدید تشکیل می دهد که دوباره مگنتیت بیشتری را به آهن فلزی احیا میکند. این چرخه واکنش تا زمانی ادامه می یابد که تمام مگنتیت به آهن فلزی تبدیل شود و بخش عمده ای از خرده کک میسوزد. به موازات چرخه احیا، سنگ آهک موجود در مخلوط احیا، گوگرد ناشی از سوزاندن خرده کک را به هم متصل می کند.
پس از احیای کامل، تجهیزات قبل از خروج از کوره به آرامی تا حدوداً 250 درجه سانتیگراد دوباره خنک می شوند. اکنون یک کیک آهنی اسفنجی لوله مانند با تخلخل حدود 75 درصد، باقیمانده خرده کک نسوخته و خاکستر غنی از گوگرد وجود دارد. در یک ایستگاه تخلیه خودکار (9)، لولههای آهن اسفنجی بیرون کشیده میشوند و خرده کک و خاکستر باقیمانده از مخزنها خارج میشوند. پس از آن، رتورت ها آماده شارژ مجدد و رفتن به یک سفر جدید از طریق کوره تونل هستند.
لوله های آهن اسفنجی در چند مرحله خرد خرد می شوند تا اندازه ذرات به زیر 3 میلی متر (10) برسد. پودر خام بهدستآمده قبل از فرآوری بیشتر، در سیلو جمع میشود. از سیلو میانی (11)، پودر خام از طریق یک زنجیره ویژه طراحی شده از جداکننده های مغناطیسی (12)، آسیاب ها (13) و صفحات (14) عبور داده می شود تا به اندازه ذرات زیر 150 میلی متر (کمتر از 100) تصفیه و جداسازی شود.
پس از آن، پودر در حال عبور از یک کوره نوار نقاله ای (15) است که در آن در دمای 800-1000 درجه سانتیگراد در هیدروژن آنیل نرم می شود و محتوای کربن و اکسیژن باقیمانده آن به سطح بسیار پایین کاهش می یابد. در طول بازپخت، پودر به یک کیک بسیار شکننده تبدیل می شود که دوباره به آرامی در آسیاب مخصوص خرد می شود. پودر به این ترتیب تراکم پذیری و استحکام خام بالایی دارد.
البته بسیاری از کوره های نوار نقاله ای برای مراقبت از حجم عظیم پودر آهنی که باید تصفیه شود در دسترس هستند. این کوره های نوار نقاله ای مدرن با گرمایش الکتریکی ویژه برای این منظور طراحی شده اند، عرض تسمه 1500 میلی متر است. پودر حاصل از چندین کوره نوار نقاله ای در یک سیلو مخصوص (16) جمع آوری می شود و در آنجا به مقدار 60 یا 120 تن همگن می شود(17).
فرآیند اتمیزه کردن آبی هوگاناس
یک کارخانه اتمیزه سازی مدرن هوگاناس AB در هالمستاد، یک شهر ساحلی کوچک در 80 کیلومتری شمال هوگاناس واقع شده است. مواد خام برای این فرآیند، ضایعات آهن و آهن اسفنجی است که با دقت انتخاب شده است. این ماده خام (1) در یک کوره قوس الکتریکی با ظرفیت 50 تن (2) ذوب می شود که در صورت تمایل می توان عناصر آلیاژی را اضافه کرد.
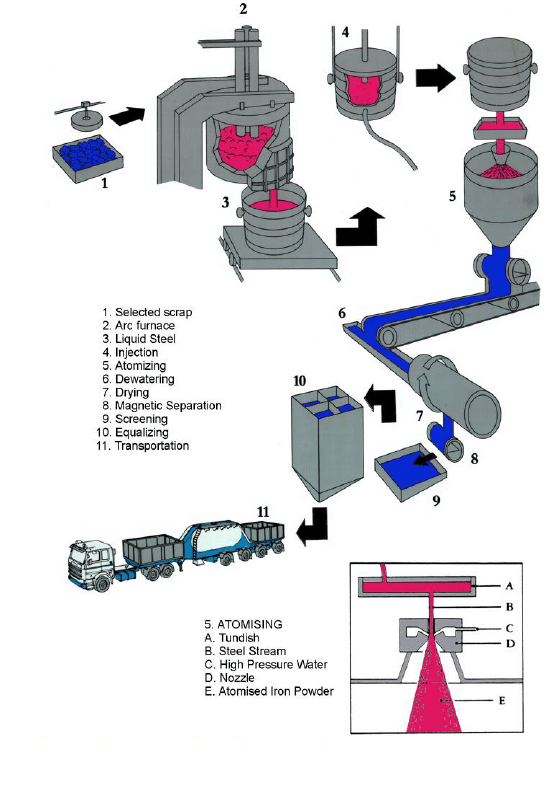
مذاب بدون سرباره از طریق سوراخ زیرین به یک ملاقه (3) منتقل می شود و در آنجا با یک نیزک اکسیژن (4) تصفیه می شود. سپس ملاقه به ایستگاه اتمیزه کردن (5) منتقل میشود و آهن مذاب(یا فولاد) بدون سرباره از طریق سوراخ پایینی در ملاقه به یک تاندیش یا پیاله بارریزی(A) با طراحی خاص ریخته میشود.
از آنجا، آهن مذاب(یا فولاد) در یک جریان خوب کنترل شده (B) از طریق مرکز یک نازل حلقهای شکل (D) جریان مییابد، جایی که توسط جتهای آب با فشار بالا (C) برخورد میکند. جریان آهن مذاب(یا فولاد) اصطلاحا به قطرات ریز (E) منفجر می شود. برخی از این قطرات بلافاصله به صورت کره های کوچک منجمد می شوند، برخی دیگر در حین انجماد در آگلومراهای کوچک با شکل نامنظم متحد می شوند.
هوا توسط جت آب حرکت می کند و بخار آب ناشی از فرآیند اتمیزه کردن باعث اکسیداسیون سطحی قطرات کوچک می شود. قطرات جامد شده و آب اتمیزه شده در یک ظرف بزرگ جمع می شوند و در آنجا به صورت گل در حال ته نشین شدن هستند. این گل پودری آبگیری (6) و خشک می شود (7).
پودر خشک به صورت مغناطیسی از ذرات سرباره جدا (8)، غربال (9) و همگن می شود (10) و در نهایت در ظروف مخصوص (11) برای پردازش و بررسی بیشتر به محل کار منتقل می شود. در حالت خروج از اتمیزه کردن، ذرات پودر اتمیزه شده نه تنها به صورت سطحی اکسید می شوند، بلکه بسیار سخت نیز می شوند، زیرا به دلیل سرعت خنک کنندگی بسیار بالا که در فرآیند اتمیزه کردن وجود دارد، به حالت مارتنزیتی منجمد شده اند(علی رغم محتوای کربن کمشان)
تاریخچه پیدایش و استفاده از پودر آهن
تولید صنعتی پودر آهن در سال 1937 با انگیزه شرکت جنرال موتورز در ایالات متحده آغاز شد. هوگاناس از سال 1922 در تولید آهن اسفنجی باکیفیت فعال بود تا در صنعت فولاد، سوئد از جهت تامین ذوب با خلوص بالا برای تولید فولادهای خاص مانند فولاد ابزار و فولاد زنگ نزن استفاده شود.
آزمایشات اولیه در سال 1937 نشان داد که به دلیل تخلخل بالا، آهن اسفنجی تولید شده توسط هوگاناس می تواند به راحتی به پودر آهن تبدیل شود. تولید پودر آهن در مقیاس کوچک در Höganäs در سوئد بین سال های 1937 و 1939 آغاز شد و ارسال منظم به ایالات متحده انجام شد.
این گریدهای اولیه پودر آهن اسفنجی بازپخت نشده حاوی حداکثر 2٪ اکسیژن قابل احیا (H2-loss) یا افت هیدروژن و تا 0.15٪ کربن بودند. در نتیجه، تراکم پذیری آنها ضعیف بود و احیای اکسیدهای باقیمانده باید در فرآیند تف جوشی(زینترینگ) تحت مصرف کربن موجود در قطعه فشرده صورت می گرفت. در چنین شرایطی، استفاده از کربن به عنوان عنصر آلیاژی غیرممکن بود. چگالی ظاهری (دانسیته ظاهری) این گریدهای پودری نسبتاً کم ، یعنی 2.2 تا 2.4 گرم بر سانتیمتر مکعب بود.
پس از سال 1940، هوگاناس روش بازپختی را معرفی کرد که در آن پودر آهن خام تحت آمونیاک تفکیک شده (75% H2 + 25% N2) حرارت داده میشد که منجر به احیای قابل ملاحظهای از اکسیژن و کربن باقیمانده میشد و تراکمپذیری بالاتری را به همراه داشت. این گرید پودری بهبودیافته با نام MH100.24 معامله شد که همان گرید NC100.24 امروزی است.
در طول جنگ جهانی دوم، متالورژی پودر آهن در آلمان پیشرفت چشمگیری داشت، جایی که به دلیل کمبود مس، نوارهای محرک گلوله توپ (فشرده و زینتر شده از پودر آهن ساده) در مقادیر بسیار زیادی تولید شد که در سال 1944 به 30000 تن متریک در سال رسید.
پودر آهن برای این منظور عمدتاً از آسیاب سیم های بریده شده و ورق های بریده در آسیاب های چکشی از نوع “همتاگ” تهیه می شد. در این فرآیند پودری به دست میاید که برای کاربرد مناسب بوده و تولید چنین پودری در چکسلواکی تا سالهای 1987-1989 ادامه یافت. با این حال، هزینه های تولید آنقدر بالا بود که این فرآیند در اروپای غربی پس از جنگ بسیار کوتاه بود.
در ارتباط با تلاش های جنگی، سایر فرآیندهای پودر آهن نیز در آلمان توسعه یافتند. مهمترین آنها فرآیند به اصطلاح RZ (روهایزن-زاندر-ورفاهرن) بود که توسط Mannesmann AG توسعه یافت که آهن ریخته گری شده و گوگرد زدایی شده توسط جت های هوا اتمیزه شد.
پودر حاصل، حاوی توده های کوچکی از ذرات کروی است که دارای سطحی به شدت اکسیدی و هسته ای حاوی کربن دارند. این پودر خام در جعبههای آهنی دربسته گرم میشد و اکسید بر روی سطح ذرات با کربن موجود در هسته واکنش میداد و در نتیجه یک اتمسفر احیایی مونوکسید کربن در داخل جعبهها ایجاد میشد. پس از این روش، پودری با سطح اسفنجی و یک هسته فشرده ایجاد شد. به دلیل سطح اسفنجی ذرات آهن، پودر دارای استحکام قبل از پخت خوبی بود، اما به دلیل وجود مقادیر نسبتا بالای اکسیدهای باقیمانده، تراکم پذیری ضعیفی داشت.
تولید و استفاده از پودرهای آهن نوع RZ امروز عملاً متوقف شده است. با این حال، یک نسخه اصلاح شده از فرآیند قدیمی RZ توسط شرکت پودر فلز کبک کانادا برای تولید برخی از گریدهای پودر Atomet استفاده شد. همچنین در اینجا، اساس فرآیند یک آهن ریخته گری است که متفاوت از فرآیند RZ قدیمی، به جای جت هوا توسط یک جت آب اتمیزه می شود. پودر خام حاصل آسیاب و با اکسید آهن مخلوط می شود. در فرآیند بازپخت بعدی و در شرایط احیایی، کربن و اکسیژن از مخلوط حذف میشوند. اگرچه این نوع پودر هنوز در حال تولید است، اما به تدریج جای خود را به انواع پودری می دهد که از اتمیزه کردن آب مذاب آهن کم کربن بدست می آیند.
بلافاصله پس از جنگ، Husqvarna Vapenfabriks AB سوئد فرآیند پودر آهن را بر اساس آهن الکترولیتی توسعه داد. این پودر آهن الکترولیتی، بسیار خالص و دارای قابلیت تراکم عالی، برای تولید قطعات با چگالی بالا بسیار مناسب است. با این حال، به دلیل هزینه ساخت بالا، بازار بسیار محدودی پیدا کرد و تولید آن در اوایل دهه هفتاد متوقف شد.
از سال 1950، پودرهای آهن اسفنجی Höganäs نیز توسط Hoeganaes Corporation در Riverton، N.J.، ایالات متحده تولید شده است. در سال 1958، Esamann AB از سوئد، تولید کننده الکترودهای جوشکاری، شروع به تولید پودر آهن با اتمیزه کردن آهن مذاب کم کربن کرد. این پودر دارای چگالی ظاهری بالایی بود و به عنوان جزئی در پوشش الکترودهای جوشکاری شرکت استفاده می شد.
در سال 1962، شرکت A.O.Smith در ایالات متحده آمریکا برای اولین بار از اتمیزه کردن آهن مذاب کم کربن و فولاد زنگ نزن کم کربن و به دنبال آن فرآیند بازپخت برای تولید پودر برای قطعات ساختاری متخلخل استفاده کرد. این پودرها فوراً به موفقیت دست یافتند، زیرا به دلیل تراکم پذیری بالا، امکان تولید قطعات با چگالی بالا با کیفیت عالی را فراهم کردند.
منابع:
https://imp-india.com/iron-powders-chemical-applications/
PRODUCTION OF IRON AND STEEL POWDERS
جهت سفارش با ما در ارتباط باشید