چهار فرآیند اصلی در تولید پودر مورد استفاده قرار می گیرد: احیای حالت جامد، اتمیزه کردن، الکترولیز و شیمیایی.
1. پودر اتمیزه(اتمایز) به چه معناست؟
پودر اتمیزه پودری است که از پراکندگی یک ماده مذاب به ذرات ریز توسط یک جریان گاز یا مایع به سرعت در حال حرکت یا توسط پراکندگی مکانیکی تولید می شود. پودرهای اتمیزه پودرهایی هستند که به روش اتمیزه کردن تولید می شوند. بیشتر پودرهای اتمیزه شده آنیل می شوند که به کاهش محتوای اکسید و کربن پودر کمک می کند.
اتمیزه کردن روش غالب برای تولید پودرهای فلزی و آلیاژی از جمله موارد زیر است:
آلومینیوم
برنج
اهن
فولادهای کم آلیاژ
فولادهای ضد زنگ
فولادهای ابزار
سوپرآلیاژها
مزایای پودرهای اتمیزه شده عبارتند از:
عمر مفید بیشتر/کاهش هزینه های چرخه عمر
مقاومت در برابر سایش بیشتر
خواص برتر در دمای بالا
افزایش انعطاف پذیری طراحی
ماشینکاری بهبود یافته
2. استفاده از روشهای اتمیزه کردن پودر فلز برای ساخت مدرن قطعات
افزایش مطالعه بر روی تکنیک های تولید قطعات با استفاده از پودرهای فلزی، از جمله تولید افزایشی (AM)، قالب گیری تزریقی فلز (MIM) و پرس ایزواستاتیک گرم (HIP)، باعث پیشرفت روشهای ساخت پودرهای فلزی آلیاژی بهویژه آلیاژهای مبتنی بر آهن، نیکل و کبالت شده است.
خواسته های جدیدتر فن آوری های متالورژی پودر Powder Metallurgy
پس از گذشت سالهای متمادی علاقه زیاد به مطالعه در زمینه متالورژی پودر (PM) و پودرهای اتمایزه بسیار دلگرم کننده بوده است. روش های متداول ساخت قطعات متخلخل PM در دهه 1980 و 1990 طرفداران زیادی نداشت، اما در بیست سال گذشته ابتدا ظهور MIM و HIP و اخیراً AM یا چاپ سه بعدی مشاهده شد. این روش ها، در حدود ده سال گذشته، منجر به افزایش سرمایه گذاری تحقیقاتی و صنعتی در زمینه متالورژی پودر PM در سراسر جهان شده است. حجم جهانی پودر مصرفی در روش های جدید در مقایسه با تجارت قطعات PM کلاسیک که حدود 1 میلیون تن در سال پودر آهن را به خود اختصاص می دهد، هنوز اندک است، اما نرخ رشد آن ها بر حسب تناژ 10 تا 40 درصد در سال است. ظرفیت تولید پودرهای ذوب شده و اتمایزه در خلاء و گاز تنها حدود 20000 تا 30000 تن در سال است.
1.2. قالبگیری تزریقی فلز (MIM): Metal injection moulding
فن آوری های جدیدتر ویژگی های مشترک خاصی دارند، تا جایی که به کیفیت پودر مربوط می شود، اما برخی تفاوت های بسیار مهمی نیز دارند. فرآیند MIM (شکل 1) شامل مخلوط کردن پودر با پلاستیک یا موم، قالبگیری تزریقی قطعات بزرگ، حذف بایندر (چسب زدایی) و سپس تف جوشی قطعه تا فشردگی کامل ادامه میابد.
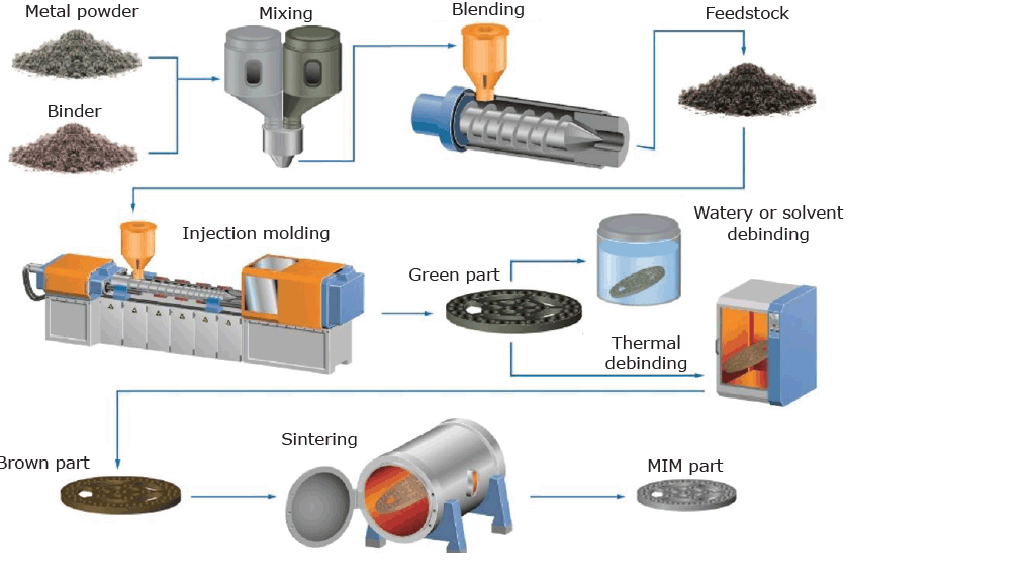
قالبگیری تزریقی فلز (MIM) یک فرآیند فلزکاری است و مراحل فرآیند شامل ترکیب پودرهای فلزی با پلیمرهایی مانند موم و بایندرهای پلی پروپیلن برای تولید مخلوط ماده اولیه است که به صورت مایع به داخل قالب با استفاده از ماشینهای قالبگیری تزریق پلاستیک تزریق میشود. قطعه قالب گیری شده یا قطعه خام، سرد شده و از قالب خارج می شود. سپس، بخشی از مواد چسبنده با استفاده از حلال، کوره های حرارتی، فرآیند کاتالیزوری یا ترکیبی از روش ها حذف می شود. بخش شکننده و متخلخل حاصله در وضعیتی قرار دارد که به آن مرحله ” برآون” می گویند. برای بهبود انتقال، اغلب جداسازی و تف جوشی(زینتر) در یک فرآیند واحد ترکیب می شوند. تف جوشی، پودر را تا دمای نزدیک به نقطه ذوب در یک کوره با اتمسفر محافظ برای متراکم کردن ذرات با استفاده از نیروهای مویرگی گرم می کند. قطعات MIM اغلب در دماهای تقریباً نزدیک به ذوب نسبی در فرآیندی به نام تف جوشی فاز مایع، پخته می شوند. برای مثال، یک فولاد زنگ نزن ممکن است تا دمای 1350 تا 1400 درجه سانتیگراد (2460 تا 2550 درجه فارنهایت) گرم شود. که نرخ نفوذ بالا است و منجر به انقباض و تراکم زیاد می شود. اگر در خلاء انجام شود، رسیدن به چگالی جامد حدود 96-99٪ معمول است. فلز محصول نهایی دارای خواص مکانیکی و فیزیکی قابل مقایسه با قطعات آنیل شده ساخته شده با روش های فلزکاری کلاسیک است. عملیات حرارتی مانند آبکاری، بازپخت، کربورسازی، نیتریدینگ و سخت شدن پس از تف جوشی برای MIM نیز مانند سایر روش های ساخت قابل انجام است.
رفتار مواد اولیه MIM با مطالعه رئولوژی، سرباره ها، سوسپانسیون ها و سایر سیالات غیر نیوتنی کنترل می شود.
برای تغذیه یا مواد اولیه MIM می توان از فلزات زیادی استفاده شود، اما رایج ترین آنها فولادهای زنگ نزن هستند که به طور گسترده در متالورژی پودر استفاده می شود. پس از قالبگیری اولیه، بایندر ماده اولیه حذف میشود و ذرات فلزی با نفوذ به یکدیگر میپیونند و متراکم میشوند تا به خواص استحکام مورد نظر دست یابند. عملیات دوم معمولاً محصول را 15٪ در هر بعد کوچک می کند.
MIM در سراسر دهه 1990 به رسمیت شناخته شد. در فناوری MIM به دلیل تولید تناژ بالا با “خلوص خالص” و حذف عملیات پرهزینه و اضافی مانند ماشینکاری هزینه های کلی به مرور کاهش یافته است، اگرچه MIM از نظر مشخصات ابعادی دارای عملکرد ضعیفی است.
MIM بیش از هر روش دیگر به پودرهای ریز نیاز دارد تا بتواند درجه بالایی از فعالیت زینترینگ را داشته باشد تا قطه خام با چگالی بالا پخته شود. پودرهای معمولی دارای اندازه ذرات متوسط 5-15 میکرومتر با حداکثر اندازه ذرات از 15 میکرومتر تا 50 میکرومتر هستند. شکل پودرهای مورد استفاده دارای انواع مختلف میباشد. با این وجود ذرات کروی و بیش از حد صاف میتوانند « brown strength» را کاهش دهند که در واقع استحکام اجزا پس از جدا شدن است. در این روش نیاز به پودرهایی با خلوص متوسط است، برای مثال محتوای اکسیژن مهم نیست، زیرا تف جوشی در دمای بالا باعث کاهش اکسیدها می شود. آلیاژها شامل فولادهای کم آلیاژ، بسیاری از فولادهای زنگ نزن (حدود 50 درصد بازار) و برخی از سوپرآلیاژها مانند IN718 هستند. اتمیزه کردن آب به طور گسترده برای فولادهای ضد زنگ استفاده می شود، اما سوپرآلیاژها به اتمیزه کردن گاز بی اثر خلاء (VIGA) نیاز دارند.
مزایا
امکان ساخت اشکال پیچیده
امکان ساخت قطعات میکرو سایز در حجم بالا
( امکان دستیابی به ویژگیهای داخلی اشکال قطعه مانند رزوههای داخلی و خارجی، سوراخهای پروفیلشده و بافتهای سطحی با جزییات دقیق، خنجر، حکاکیها و نشانهها وجود دارد.)
معایب
هزینه اولیه بالاتر: در فرآیند MIM به دلیل ساخت ابزار، سرمایه گذاری اولیه بالایی مورد نیاز است.
محدودیت اندازه: MIM برای قطعات کوچکتر بسیار خوب است اما در حال حاضر امکان ساخت قطعات بیش از 20 سانتی متر در فرآیند MIM وجود ندارد.
مقدار: MIM تنها در صورتی مناسب است که نیازهای کمیت بالاتر وجود داشته باشد.
2.2. پرس ایزواستاتیک گرم (HIP): Hot isostatic pressing
پرس ایزواستاتیک گرم (HIP) یک فرآیند تولیدی است که برای کاهش تخلخل فلزات و افزایش چگالی بسیاری از مواد سرامیکی استفاده می شود. این روش باعث بهبود خواص مکانیکی و کارایی مواد می شود.
فرآیند HIP (شکل 2) شامل پر کردن ظروف فلزی قوطی مانند با پودر است که پس از تخلیه هوا و آب بندی، به صورت ایزواستاتیک گرم تحت فشار قرار می گیرند، معمولاً در فشارهای 1000-2000 بار و دمای 1000 -1200 درجه سانتیگراد.
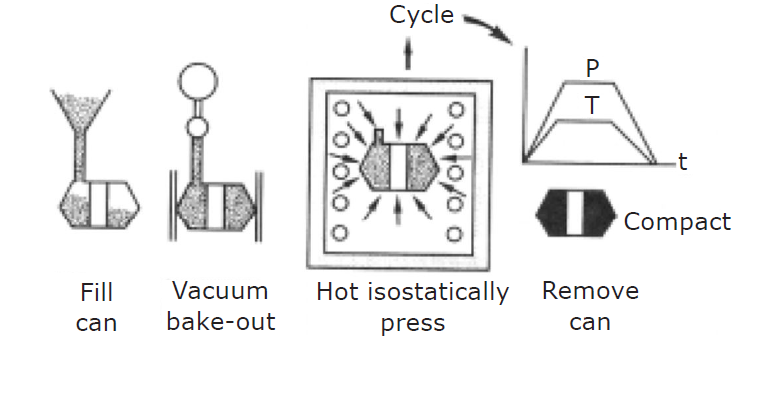
این امر مستلزم چگالی ضربهای بالا و قابل تکرار برای کاهش انقباض (معمولاً 10-15٪) در فشار است، اشکال ذرات مورد استفاده کروی و صاف بوده که برای کمک به پر کردن قوطیهای شکلدار بسیار مطلوب است.
خلوص در این مورد بسیار مهم است، زیرا هیچ تغییری در محتوای اکسیژن در HIP امکان پذیر نیست. بنابراین استفاده از پودرهای اتمیزه شده گازی برای این کار تقریباً اجباری است. اندازه ذرات دارای اهمیت ثانویه است، اگرچه برای کاربردهای ضروری از جمله هوافضا، پودرهای ریز، معمولاً کمتر از 53 میکرومتر، استفاده میشود. آلیاژهای مورد استفاده از فولادهای زنگ نزن و ابزار گرفته تا سوپرآلیاژها را شامل می شود. فرآیند HIP یک قطعه را در معرض دمای بالا و فشار ایزواستاتیک در یک مخزن فشار بالا قرار می دهد. گاز تحت فشاری که بیشتر مورد استفاده قرار می گیرد آرگون است که یک گاز بی اثر است تا مواد باهم واکنش شیمیایی نشان ندهند. بسیاری از سیستم ها از پمپاژ گاز مرتبط برای رسیدن به سطح فشار لازم استفاده می کنند. فشار از همه جهات به مواد اعمال می شود (از این رو اصطلاح “ایزواستاتیک”به کار میرود).
3.2. تولید افزودنی (AM) : Additive manufacturing
تولید افزودنی (AM) یا تولید لایه افزودنی (ALM) نام تولید صنعتی برای چاپ سه بعدی است، یک فرآیند کنترل شده توسط کامپیوتر که با رسوب دادن مواد، معمولاً در لایه ها، اشیاء سه بعدی ایجاد می کند.
فرآیندهای تولید افزودنی
تعدادی فرآیند AM متمایز با استانداردهای خاص خود وجود دارد که عبارتند از:
- بایندر جتینگ
این تکنیک از یک هد چاپ سه بعدی که بر روی محورهای x، y و z حرکت میکند، استفاده میکند تا لایههای متناوب مواد پودری و یک چسب مایع را به عنوان چسب قرار دهد.
- رسوب مستقیم توسط انرژی
تولید مواد افزودنی با رسوب مستقیم توسط انرژی را می توان در طیف گسترده ای از مواد از جمله سرامیک، فلزات و پلیمرها استفاده کرد. یک لیزر، قوس الکتریکی یا یک تفنگ پرتو الکترونی نصب شده بر روی یک بازو، سیم ذوب، مواد اولیه رشته یا پودر را به صورت افقی حرکت میدهد تا در حالی که بستر به صورت عمودی حرکت میکند، مواد ایجاد کند.
- اکستروژن مواد
این فرآیند متداول AM از پلیمرهای قرقره ای استفاده می کند که یا اکسترود می شوند یا از طریق یک نازل گرم شده که روی یک بازوی متحرک نصب شده کشیده می شوند که مواد ذوب شده را لایه به لایه می سازد زیرا نازل به صورت افقی و بستر به صورت عمودی حرکت می کند. لایه ها از طریق کنترل دما یا عوامل پیوند شیمیایی به هم می چسبند.
- نفوذ بستر پودری
همجوشی بستر پودری شامل انواع تکنیک های AM از جمله ذوب فلزات با لیزر مستقیم (DMLM)، تف جوشی(پخت) لیزری مستقیم فلزات (DMLS)، ذوب با پرتو الکترونی (EBM)، تف جوشی لیزری انتخابی (SLS) و تف جوشی حرارتی انتخابی (SHS) می باشد. پرتوهای الکترونی، لیزرها یا هدهای چاپ حرارتی برای ذوب یا ذوب بخشی از لایههای ریز مواد استفاده میشوند که پس از آن پودر اضافی خارج میشود.
- لمینیت ورق
لمینیت ورق را می توان به دو فناوری تقسیم کرد. ساخت اشیای چند لایه (LOM) و تولید مواد افزودنی اولتراسونیک (UAM). تولید اشیاء چند لایه برای ایجاد اقلامی با جذابیت بصری یا زیبایی شناختی مناسب است و از لایه های متناوب کاغذ و چسب استفاده می کند. UAM از جوشکاری اولتراسونیک برای اتصال ورق های فلزی نازک استفاده می کند.در یک فرآیند کم انرژی و دمای پایین، UAM را می توان از فلزات مختلف مانند آلومینیوم، فولاد ضد زنگ و تیتانیوم استفاده کرد.
- پلیمریزاسیون Vat
این فرآیند از یک فتوپلیمر رزین مایع برای ایجاد یک جسم لایه به لایه استفاده می کند. از آینه ها برای هدایت نور فرابنفش استفاده می شود که لایه های متوالی رزین را از طریق فتوپلیمریزاسیون خشک می کند.
- تولید افزودنی قوس سیمی (اکنون به عنوان رسوب انرژی مستقیم-قوس (DED-arc) شناخته می شود)
در تولید افزودنی قوس سیمی از منابع انرژی جوش قوس الکتریکی و دستکاریکنندهها برای ساخت اشکال سه بعدی از طریق رسوب قوس استفاده میشود. این فرآیند معمولاً از سیم به عنوان منبع مواد استفاده می کند و یک مسیر از پیش تعیین شده را برای ایجاد شکل مورد نظر دنبال می کند. این روش ساخت افزودنی معمولاً با استفاده از تجهیزات جوشکاری رباتیک انجام می شود.
زمینه AM در تقاضاهای خود نسبتاً متنوع تر است بزرگترین روش در حال حاضر، تف جوشی لیزری است که نام های مختلفی دارد، این روش در شکل 3 نشان داده شده است. این فرایند همانطور که گفته شد به پودرهایی با خاصیت جریان عالی نیاز دارد تا به پخش شدن پودر در لایه های نازک قبل از زینترینگ یا به طور دقیق تر جوشکاری شکل قطعه کمک کند. محتوای اکسیژن نیز بسیار مهم است که در تلاشند از پودرهای اتمیزه شده در آب استفاده کنند اما فعلا روش ، اتمیزه کردن گاز در این زمینه غالب است. یک ویژگی بسیار مهم این است که اندازه ذرات محدوده ی خاصی دارد که به صورت اسمی بین 53- 23+میکرومتر یا 45- 15+ میکرومتر تنظیم شده است. بنابراین بازده در این محدوده اندازه ذرات تأثیر عمده ای بر هزینه های تولید پودر دارد.
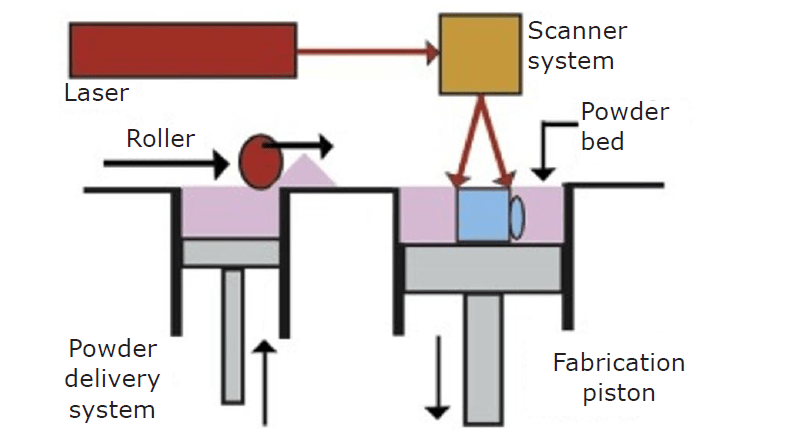
فرآیندهای AM دیگری که در دهه گذشته توجه زیادی را به خود جلب کرده اند بایندرجتینگ است که از پودرهای “MIM-grade” استفاده می کنند (شکل 4).
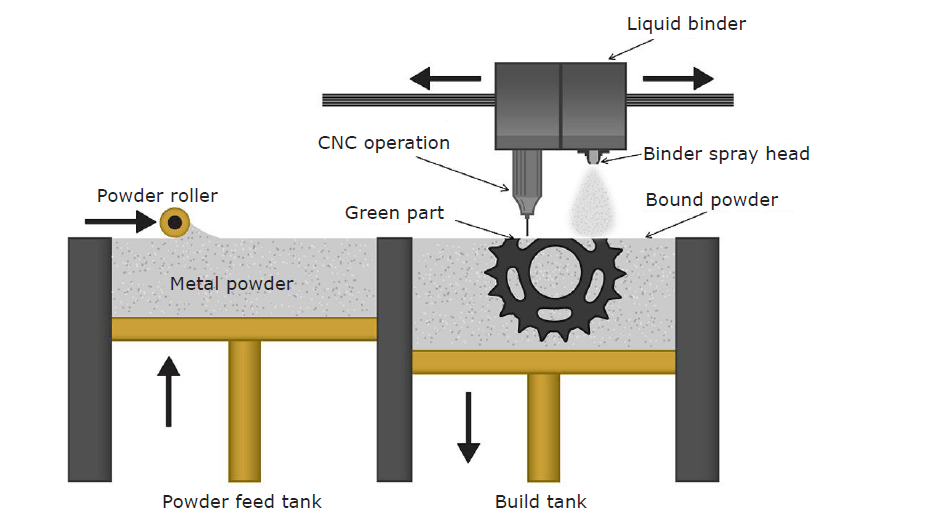
3. فرآیندهای اتمی سازی (اتمایزه کردن)
اتمیزه شدن تجزیه یک مایع به یک حالت اسپری مناسب است. روش های زیادی برای اتمیزه کردن یک فلز وجود دارد، اما برای روش های ساخت مدرن که در اینجا مورد بحث قرار می گیرد، فرآیندهایی که به طور گسترده مورد استفاده قرار می گیرند، اتمیزه کردن با آب و گاز است. همچنین ترکیبی از این دو، به عنوان روش اتمیزه کردن آب با فشار فوق العاده بالا ultra-high pressure (UHP) وجود دارد. ساخت قلع به عنوان پودر 10 میکرون با این روش بسیار آسان است، اما فولاد بسیار دشوارتر است. انواع روش های تولید پودر اتمایز در ادامه ذکر شده است.
1.3. اتمیزه کردن با گاز
اصطلاح اتمیزه کردن گاز در حال حاضر تعدادی از تکنیک های مختلف را پوشش می دهد. مهم ترین انواع آن اتمیزه کردن هوا، اتمیزه کردن با گاز بی اثر inert gas atomisation (IGA) و VIGA است.
1.1.3. اتمیزه کردن هوا: Air Atomisation
اتمیزه شدن هوا فرایندی است که هم اتمیزه شدن و هم ذوب شدن در هوا انجام می شود. کمپرسورهای هوای فشرده برای شکستن فلز مذاب استفاده می شود و اغلب خنک سازی با مکش حجم زیادی از هوا از طریق تجهیزات حاصل می شود. این روش به طور گسترده از سال 1900 برای ساخت پودرهای قلع، سرب، آلومینیوم و روی و همچنین برای برخی از آلیاژهای مس استفاده می شود. در اواسط قرن بیستم برای تولید آلیاژهای Fe-C نیزاستفاده می شد، اما اکنون منسوخ شده است. همانطور که انتظار می رود، محتوای اکسیژن پودرهای اتمیزه شده با هوا نسبتاً زیاد است، معمولاً در محدوده ppm-1% 1000است. اشکال ذرات از نامنظم برای Al، Zn تا کروی برای مس، طلا و نقره متغیر است. اندازه ذرات برای آلیاژهای نیکل، آهن حدود 50-200 میکرومتر، برای Sn، Pb، 10-30 میکرومتر است.
2.1.3. اتمیزه کردن گاز بی اثر: Inert Gas Atomisation
IGA فرایندی است که مذاب توسط گاز بی اثر، معمولاً نیتروژن یا آرگون، تجزیه می شود و در نتیجه از اکسیداسیون محافظت می شود. این روش در دوره پس از جنگ جهانی دوم با ذوب شدن در هوا توسعه یافت و برای طیف بسیار وسیعی از آلیاژها از Sn و Pb تا آلیاژهای طلا، نقره، مس، کبالت، نیکل و آهن استفاده شد.
زمینه های اصلی کاربرد این تکنیک پودرهای اسپری حرارتی، هارد فیسینگ(پوشش سخت)، لحیم کاری، دندانپزشکی و اخیراً HIP، MIM و AM بوده است. محتوای اکسیژن می تواند بسیار کمتر از پودرهای اتمیزه شده با هوا باشد، معمولاً در محدوده 100-500 ppm و بسیار وابسته به آلیاژ است. اشکال ذرات به طور معمول کروی هستند، اما تجمع(آگلومره شدن) و دندریت شدن ممکن است رخ دهد. اندازه متوسط ذرات معمولاً 30 تا 200 میکرومتر برای آلیاژهای Fe, Ni, Co است و جهت تعیین حد بالای اندازه ذرات و به دلیل بزرگ بودن ظرف مورد استفاده جهت جلوگیری از پاشیدن قطرات بزرگتر، به مذاب روی دیواره ها توجه می شود.
3.1.3. اتمیزه کردن گاز بی اثر در خلاء: Vacuum Inert Gas Atomisation
VIGA روشی است که ذوب و ریختن آلیاژ قبل از اتمی شدن در یک محفظه خلاء انجام می شود تا امکان تولید حساس ترین آلیاژها به اکسیداسیون و واکنش پذیرترین آلیاژها، به ویژه آلیاژهای مبتنی بر آهن، نیکل، تیتانیوم، سوپرآلیاژهایی مانند IN718، فولادهای پیرسازی مارتنزیتی و آلیاژهای M-Cr-Al-Y فراهم شود. این تکنیک از دهههای 1950 و 1960 توسعه یافت، زمانی که فشاری برای کشف مزایای بالقوه انجماد سریع (RS) وجود داشت تا امکان تولید سوپرآلیاژهای برای کاربردهای هوافضا و صنایع دفاعی فراهم شود. پس از چندین دهه توسعه، اکنون هزاران تن در سال از پودرهای سوپرآلیاژ تولید شده توسط VIGA جذب می شود که به خوبی قادر به تولید پودر برای HIP، MIM و AM است. محتوای اکسیژن در محدوده 50-200 ppm قابل دستیابی است. شکل ذرات کروی بدشکل بوده و اندازه ذرات مانند IGA است.
2.3. اتمیزه کردن به روش الکترود گاز القایی: Electrode Induction Gas Atomisation
در اتمیزه کردن گاز القایی الکترود (EIGA، شکل 5) جریان مذاب توسط یک تاندیش(پیاله واریز) و نازل تامین نمی شود، ، بلکه با ذوب قطره ای یک “الکترود” (یا میله) که به آرامی چرخانده می شود تا فرآیند ذوب یکنواخت شود. سیم پیچ القایی پروفیلی که معمولاً در فرکانس بسیار بالا (بیش از 50 کیلوهرتز) کار می کند تا از نیروهای مغناطیسی هیدرودینامیکی بیش از حد بر مذاب جلوگیری کند، نوک میله به شکل کلی مخروطی ذوب می شود و جریان قطرات آلیاژ مذاب حاصل به یک نازل اتمی گاز سقوط آزاد می ریزد.
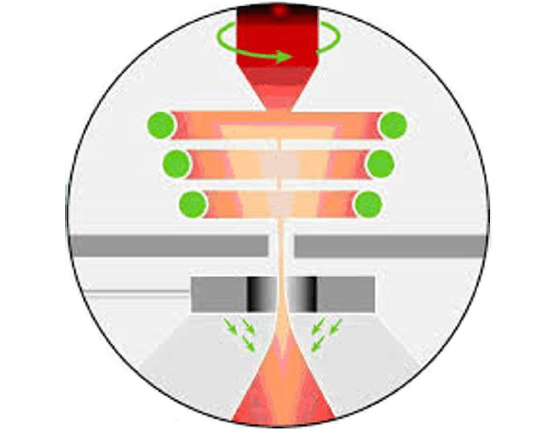
این فرآیند در حال حاضر به طور گسترده برای تولید آلیاژ Ti استفاده می شود، اما این روش موانعی هم دارد مثلا سرعت ذوب نسبتاً آهسته است، معمولاً 10-30 کیلوگرم در ساعت، که این امر منجر به مصرف بالای گاز (آرگون) به ازای هر کیلوگرم پودر و همچنین توزیع نسبتاً درشت اندازه ذرات (متوسط 40 تا 100 میکرون) می شود. شکل ذرات متناسب و شبه کروی است، اما مقداری ذرات دنذریتی نیز موجود است. اگر سیستم کاملاً تحت شرایط مهندسی خلاء باشد خلوص بسیارعالی خواهد بود.
3.3. اتمیزه شدن تحت پلاسما: Plasma Atomisation
اتمیزه کردن پلاسما (شکل 6) اصطلاحیست که تا حدودی مبهم است، اما به طور کلی برای توصیف فرآیند ابداع شده توسط Pyrogenesis در کانادا در سال 1995 و به طور گسترده برای تولید پودرهای Ti و آلیاژ Ti مورد استفاده قرار می گیرد. این فرآیند شامل وارد کردن یک سیم فلزی به کانون سه مشعل پلاسما است که ذوب شده و سپس مواد مذاب را اتمیزه میکنند.
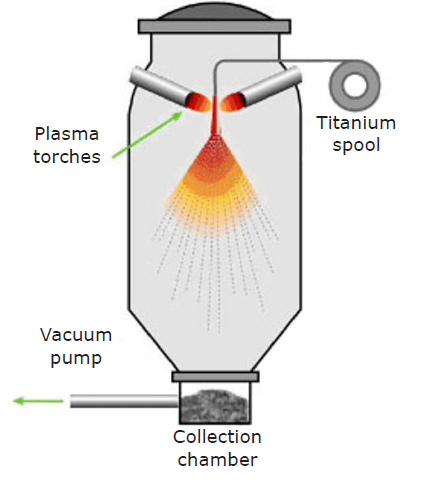
این فرآیند ارزان نیست زیرا هم مواد اولیه که سیم تیتانیم است هزینه بالایی دارد (با چند میلی متر قطر) و هم بهره وری و بازده فعلا پایین است، معمولاً 10 کیلوگرم در ساعت است، اما اخیراً ادعا شده است که به بیش از 20 کیلوگرم در ساعت افزایش یافته است. شکل ذرات بسیار کروی (به دلیل سرعت تولید بسیار پایین و جریان گاز متوسط) وبا خلوص عالی است.
4.3. اتمیزه کردن با آب: Water Atomisation
اتمیزه کردن آب (WA) روشی است که به قرن ها قبل برمی گردد. فلز مذاب توسط اسپری های آب با فشار بالا، معمولاً بین 3 تا 20 مگاپاسکال تجزیه می شود. ذوب شدن در هوا انجام می شود و اتمیزه شدن ابتدا در اتمسفر هوا انجام می شود و در نتیجه محتوای اکسیژن بسیار بالایی برای فولادها ایجاد می شود. از اواسط قرن بیستم، بیحرکتی محفظه اتمیسازی امکان تولید تناژهای عظیم پودر آهن و طیف وسیعی از فولادهای آلیاژی، از جمله فولادهای زنگ نزن و فولادهای ابزار را فراهم کرده است. همچنین به طور گسترده برای تولید آلیاژهای طلا، نقره، روی و مس و برای برخی از انواع آلیاژهای Ni و Co استفاده می شود. محتوای اکسیژن بسیار وابسته به آلیاژ است و از 500 ppm برای برخی از آلیاژهای Ni-Cr-B-Si و آلیاژهای مس تا 1٪ برای فولادهای پر منگنز متغیر است. شکل ذرات عموماً تا حدودی نامنظم است، اما به شدت تحت تأثیر ترکیب آلیاژ و شرایط اتمیزه شدن قرار می گیرد، به طوری که چگالی ظاهری(حجمی) می تواند از 20٪ تا 50٪ جامد متغیر باشد. اندازه ذرات برای فولادها از 30 میکرومتر تا 1000 میکرومتر متغیر است، زیرا خاموش شدن سریع جت های آب به ذرات بزرگتر اجازه می دهد تا به سرعت منجمد شوند.
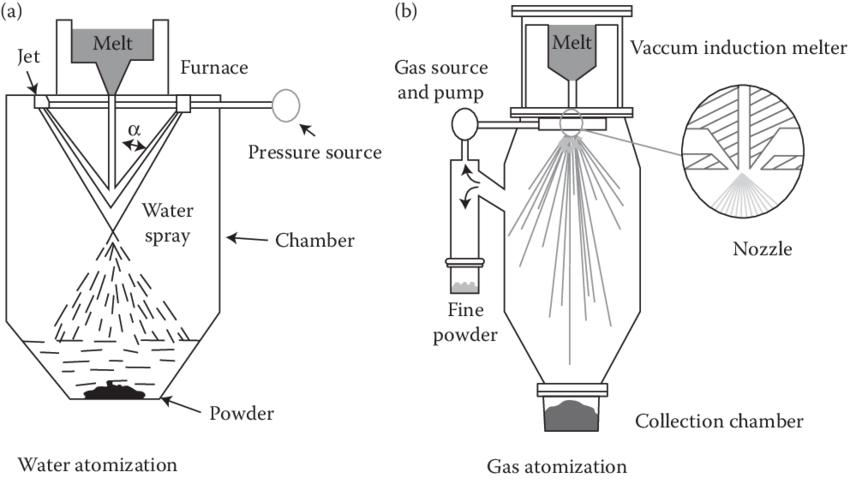
5.3. اتمیزه کردن آب با فشار فوق العاده بالا: Ultra-High Pressure Water Atomisation
اتمیزه کردن آب با فشار فوق العاده بالا (UHPWA) همانطور که از نام آن پیداست، شامل استفاده از فشارهای آب بسیار بالا، معمولاً در محدوده 100 تا 200 مگاپاسکال است. در چنین فشارهایی، جتهای آب مافوق صوت هستند و با سرعتهای 400 تا 500 متر بر ثانیه حرکت میکنند و اتمیشدن تا حدی به دلیل امواج ضربهای در اطراف جتهای آب است. معمولاً در یک محفظه اتمیزه شدن با گاز بی اثر انجام می شود و امکان تولید پودرهای فولادی بسیار ریز با اندازه ذرات متوسط حدود 10 میکرومتر را فراهم می کند. محتوای اکسیژن هم به دلیل سطح بالای چنین پودرهای ریز و هم به دلیل پتانسیل اکسیداسیون آب، معمولاً در محدوده 2000-5000 ppm است. شکل ذرات میتواند از تا حدودی نامنظم تا نسبتاً کروی متغیر باشد، که اجازه میدهد چگالی بالای 4.5 گرم در میلیلیتر برای فرایند MIM داشته باشد.
4. عوامل اصلی در انتخاب تکنیک اتمیزه کردن
برای همه روش های مختلف تولید پیشرفته مانند MIM، HIP و AM ، بازده تولید پودر با اندازه دانه صحیح یک عامل اقتصادی و حیاتی است. برای MIM، نگرانی اصلی داشتن یک پودر بسیار ریز برای فرایند پخت بالا است. مشخصات معمولی اندازه متوسط ~ 10 میکرون است. UHPWA می تواند چنین پودری را با بازدهی 70 تا 80 درصد از آن تهیه کند
پودر اتمیزه شده گاز در تلاش است تا بازدهی بیش از 50 درصد را فراهم کند. علاوه بر این، یکی از دلایل اصلی استفاده از اتمیزه کردن گاز بی اثر، دستیابی به محتوای اکسیژن کم، برای بسیاری ازسوپر آلیاژها مورد توجه است.
برای روش HIP، که (در بسیاری از موارد) نه حداقل اندازه ذرات و نه حداکثر اندازه (شاید 100 تا 300 میکرون) را محدود میکند، بازده بسیار بالا است، در محدوده 80-98%.
برای AM با استفاده از لیزر، که نیاز به توزیع فشرده معمولاً با نسبت حداکثر به حداقل 2.5-3 دارد، وسعت توزیع بسیار مهم است. پودرهای اتمیزه شده عموماً از توزیع آماری log-normal پیروی می کنند و می توانند انحراف استاندارد از 1.8 تا 2.5 یا بیشتر داشته باشند.
تفاوت در بازده در محدوده اندازه 3:1 بسیار زیاد است. برای 1.8 انحراف استاندارد (تئوری، 100٪ بررسی کارآمد) بازده می تواند به 64٪ برسد، در حالی که در 2.2 انحراف استاندارد به ~51٪ کاهش می یابد.
یک عامل مهم دیگر جریان پذیری است. این تحت تأثیر شکل ذرات است، که به شدت تحت تأثیر “satelliting” قرار می گیرد که در آن ذرات کوچکتر به ذرات بزرگتر می چسبند.
در حالت کلی سه نوع اتمیزه کردن وجود دارد:
اتمیزه شدن مایع
اتمیزه شدن گاز
اتمیزاسیون گریز از مرکز
ذرات اتمیزه شده مایع کوچکتر، تمیزتر و غیر متخلخل هستند و وسعت بیشتری دارند که امکان فشرده سازی بهتر را فراهم می کند. ذرات تولید شده از این روش معمولاً به شکل کروی یا گلابی هستند. اتمیزه کردن مایع نسبت به روش های دیگر هزینه کمتری دارد، اما محدودیت های آن عبارتند از: خلوص پودر، شکل ذرات و محتوای اکسیژن سطح.
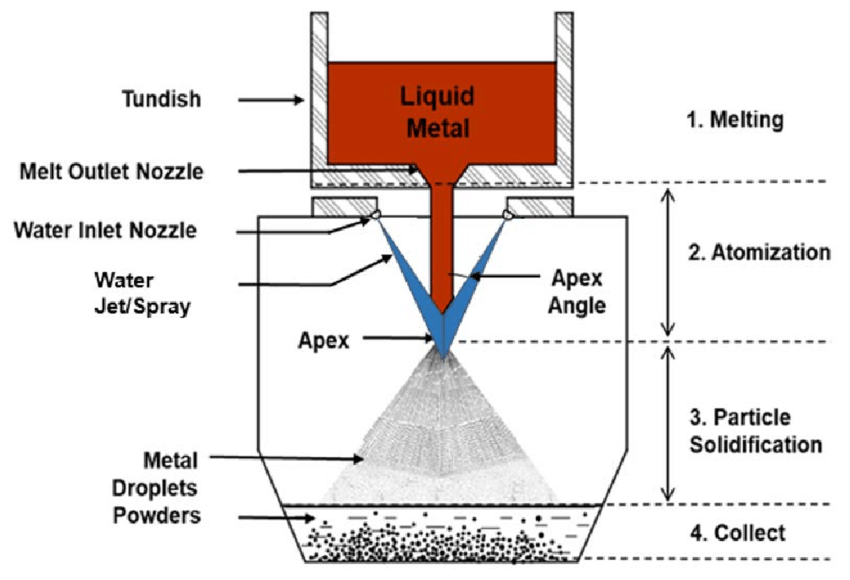
اتمیزه شدن گاز باعث تولید پودرهای فلزی با کیفیت می شود. در طی فرآیند اتمیزه شدن گاز، فولاد مذاب به قطرات فلزی ریز تبدیل می شود که در طی سقوط در برج اتمیزه سرد می شوند. پودرهای فلزی که با اتمیزه کردن گاز به دست میآیند، یک شکل کاملاً کروی همراه با سطح تمیزی بالا را ارائه میدهند. پودرهای اتمیزه شده با گاز معمولاً از نظر هندسی کروی تر هستند و محتوای اکسیژن سطح پایین تری نسبت به نمونه های اتمیزه مایع خود دارند.
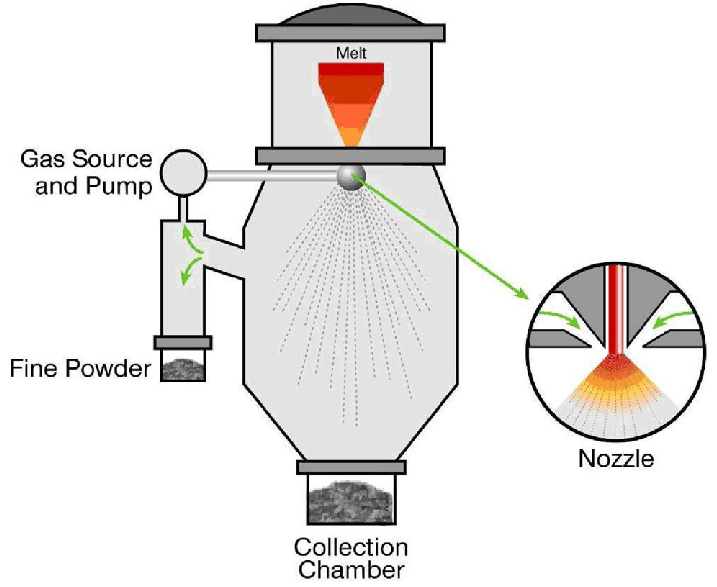
در اتمیزه کردن گریز از مرکز، یک جریان مایع توسط نیروی گریز از مرکز یک دیسک چرخان، فنجان یا الکترود به قطرات پراکنده می شود.
جهت اطلاع از مشخصات انواع پودر های اتمایز موجود میتواند به بخش پودر و مواد اولیه مراجعه بفرمایید.
منابع:
https://www.corrosionpedia.com
Dunkley JJ. Metal powder atomisation methods for modern manufacturing. Johnson Matthey Technology Review. 2019 Jul 1;63(3):226-32.