متالورژی پودر یک مسیر تولیدی جذاب برای تولید قطعات با استفاده از پودر فلزات است که از نظر اقتصادی مقرون به صرفه بوده و تولید قطعات با انواع اشکال را تسهیل می کند. متالورژی پودر امروزه به طور گسترده ای مورد استفاده قرار می گیرد و جایگزین مناسبی برای روش های قدیمی آن است. متالورژی پودر یک فرآیند تشکیل فلز است که با حرارت دادن پودرهای فلزی متراکم شده تا زیر نقطه ذوب آنها انجام می شود در واقع فرآیند متالورژی پودر شامل مخلوط کردن پودر عنصری یا آلیاژی، فشرده سازی مخلوط در قالب و سپس تف جوشی یا گرم کردن شکل حاصل در یک اتمسفر کنترل شده است. متالورژی پودر یک روش بسیار توسعه یافته برای تولید مواد آهنی و غیر آهنی است. این یک فرآیند با کمترین میزان تراشه است.
متالورژی پودر امکان پردازش مواد با نقطه ذوب بسیار بالا از جمله فلزات نسوز مانند تنگستن، مولیبدن و تانتالیوم را فراهم می کند. تولید چنین فلزاتی از طریق ذوب و ریخته گری بسیار دشوار است و اغلب در حالت ریخته گری بسیار شکننده هستند.
گردش مالی سالانه متالورژی پودر در بازار اروپا بیش از شش میلیارد یورو است، حتی تولید جهانی پودر فلز بیش از یک میلیون تن است. جدا از روش ریخته گری که فقط در فلزات زود گداز قابل استفاده است، روش متالورژی پودر تقریباً در همه مواد قابل اجرا است. بیشتر محصولاتی که با استفاده از روش متالورژی پودر تولید می شوند، نمی توانند با روش ریخته گری تولید شوند.
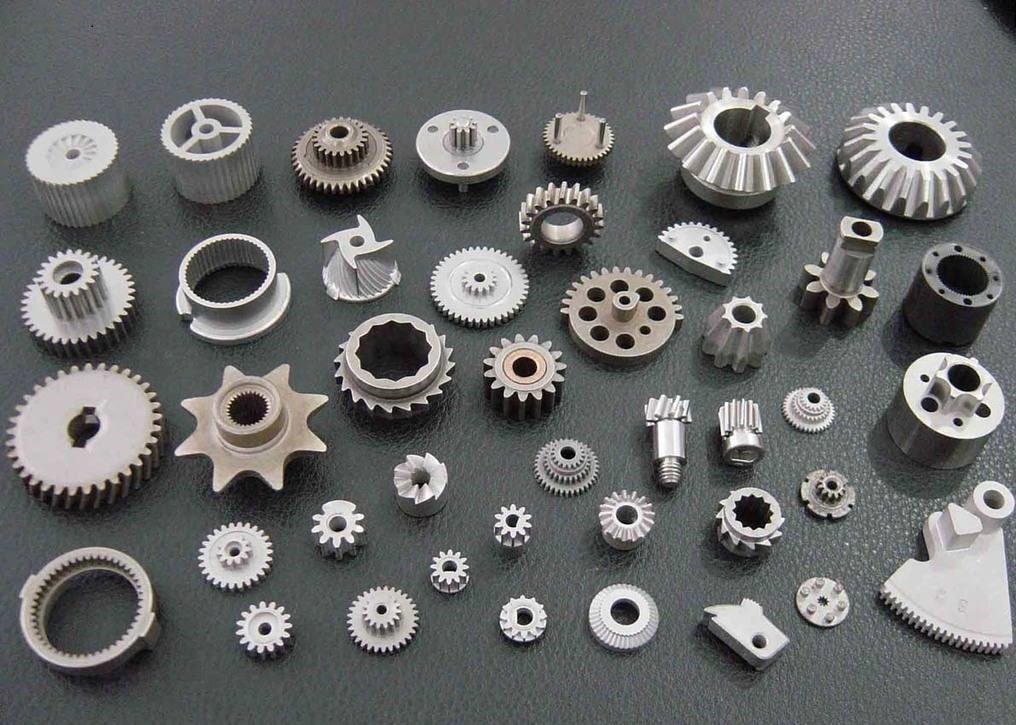
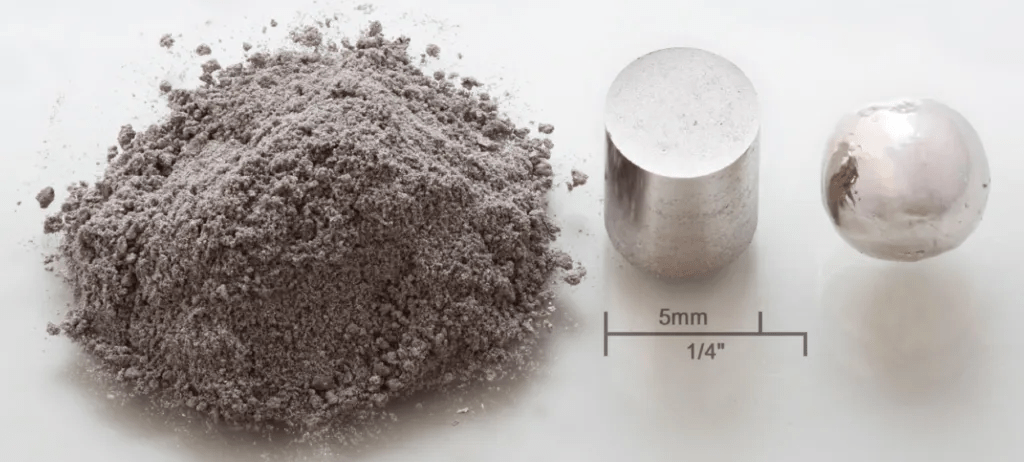
در زمینه مهندسی، همیشه قصد تولید قطعات فلزی بسیار دقیق وجود دارد. اما در برخی مواقع تولید قطعات فلزی مورد نیاز به کمک روش های معمولی بسیار مشکل است. از این رو در شرایط سخت از متالورژی پودر استفاده می شود. مشاهده می شود که این فرآیند تولید فلز در دوران باستان اختراع شده است. اما مردم از قرن نوزدهم شروع به استفاده از این روش کردند.
متالورژی پودر (PM) تولید و استفاده از پودرهای فلزی است. پودرها به ذراتی گفته می شود که معمولاً اندازه آنها کمتر از 1000 نانومتر (1 میلی متر) است. بیشتر ذرات فلزی مورد استفاده در PM در محدوده 5 تا 200 میلی متر قرار دارند. برای بیان این موضوع، موی انسان معمولاً در محدوده 100 میلیمتر (3.9 میلیمتر) قرار دارد.
صنعت پودر فلز، یک فناوری شناخته شده شکل دهی فلز است که به طور مستقیم با سایر روش های فلزکاری مانند ریخته گری، آهنگری، مهر زنی (ریز خالی کردن) و ماشینکاری پیچ رقابت می کند. این صنعت شامل تامین کنندگان پودر و قطعه سازان، به علاوه شرکت هایی است که تجهیزات اختلاط، تجهیزات جابجایی پودر، پرس های متراکم، کوره های تف جوشی و غیره را تامین می کنند. فرآوری متالورژی پودر مزایای زیادی دارد. فرآیند PM در مقایسه با سایر فنآوریهای شکلدهی فلزات، در مواد و انرژی کارآمد است.
متالورژی پودر برای ساخت قطعات با شکل پیچیده مقرون به صرفه است و نیاز به ماشینکاری را به حداقل می رساند. طیف وسیعی از مواد مهندسی شده در دسترس است و از طریق انتخاب مواد و فرآیند مناسب، ریزساختار مورد نیاز ممکن است در مواد ایجاد شود. قطعات متالورژی پودر سطح خوبی دارند و ممکن است برای افزایش استحکام یا مقاومت در برابر سایش عملیات حرارتی شوند.
در صورت لزوم، ریز تخلخل کنترل شده می تواند برای خود روانکاری یا فیلتراسیون ارائه شود. در حالی که دقت ابعاد خوب است، معمولاً با قطعات ماشینکاری شده مطابقت ندارد. در مورد قطعات PM آهنی، در مقایسه با فولاد ریخته گری نشده ، شکل پذیری کمتر و مقاومت ضربه ای کمتری دارند. اکثر قطعات PM متخلخل هستند و هنگام انجام عملیات تکمیلی باید به آن توجه شود.
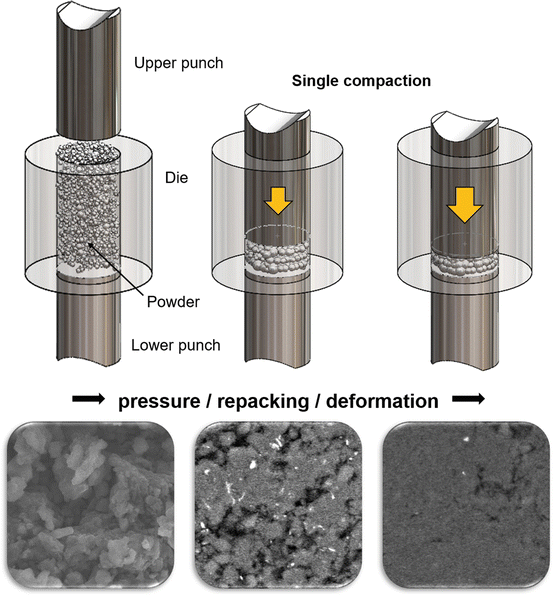
فرآیند های متالورژی پودر:
1- تولید پودر
متالورژی پودر شامل فرایندی است که با انتخاب ماده اولیه آغاز می شود و تا زمانی که به محصول نهایی تبدیل شود ادامه می یابد. فرآیند متالورژی پودر تولید محصولات بسیار پیچیده را امکان پذیر می کند. مرحله اول با انتخاب پودر شروع می شود. پودر انتخاب شده با توجه به نیاز قطعه تولید می شود. خواص پودر برای خصوصیات قطعه ای که باید تولید شود مهم است.
2- مخلوط کردن پودر تولید شده
پودر خام با برخی از عناصر آلیاژ و با افزودن روان کننده یا برخی مواد افزودنی خاص مخلوط می شود. مخلوط کردن تا زمانی که مخلوطی همگن حاصل شود انجام می شود. این ترکیب در تعیین خصوصیات ماده از اهمیت زیادی برخوردار است.
3- فشرده سازی (Compaction)
هدف از این مرحله، قرار دادن مخلوط پودر بدست آمده در قالب ها و رساندن آنها به شکل و اندازه لازم است. شکل دهی با تراکم و مقاومت کافی با فشارهای مکانیکی یا هیدرولیکی انجام می شود.
مرحله دوم در متالورژی پودر، فشرده سازی پودر است که فشار بالایی برای فشرده سازی پودر فلز در قالب اعمال می شود.
در این فرآیند با وارد شدن فشار زیاد به پودر، چگالی پودر تغییر می کند. برای فشرده سازی پودر فلز، فشار از 150 MPa تا 700 MPa متغیر است. در فشرده سازی، فرآیند پرس کاری قالبی باید در نظر گرفته شود.
پرس کاری قالبی معروف ترین روش تولید محصولات از پودر آنهاست که در قالب پرس چهار مرحله وجود دارد:
1- حفره قالب با پودر پر می شود.
2- فشردگی این پودر صورت می گیرد.
3- از پانچ پایینی برای فشرده سازی پودر استفاده می شود.
4- کمپکت (قطعه فشرده) باقی مانده از سطح بالایی قالب حذف می شود.
4- تف جوشی (زینترینگ)
این مرحله فرآیند شامل قطعات گرم شده در جو محافظ با دمای کمتر از دمای ذوب است. در نتیجه فرآیند، ساختار متخلخل در قطعه از بین می رود و به طور پایدار قدرت و سفتی پیدا می کند. علاوه بر این، تشکیل پیوند تبلور و رشد در ساختار ذرات پودر دیده می شود.
در زینترینگ، قطعه فشرده تشکیل شده (که به آن محصول سبز نیز می گویند) در زیر نقطه ذوب خود، در دمای مناسب برای مدت زمان معین و در حضور گازهای مناسب گرم می شود. هدف اصلی از تف جوشی حذف روان کننده، تشکیل دوباره روان کننده و جلوگیری از اکسیداسیون است.
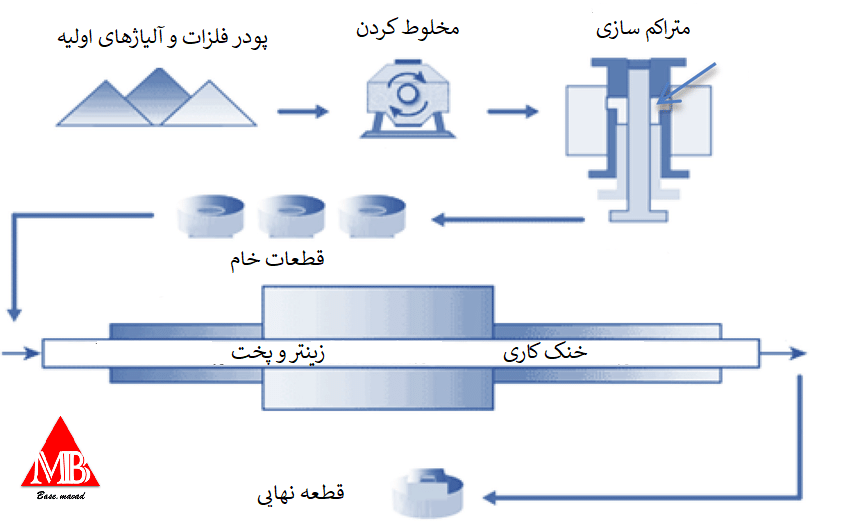
دمای پخت(زینتر) برای مواد مختلف
مواد | دما (درجه سانتی گراد) |
مس، برنج، برنز | 760-900 |
نیکل | 1000-1150 |
فولاد زنگ نزن | 1100-1290 |
فریت ها | 1200-1500 |
کاربید تنگستن | 1430-1500 |
مولیبدن | 2050 |
تنگستن | 2350 |
تانتالیوم | 2400 |
عملیات ثانویه مربوط به متالورژی پودر
پس از پخت، قطعه تولید شده باید عملیات ثانویه مختلفی را طی کند تا قطعه نهایی و تمام شده تولید شود. تمام عملیات ثانویه ضروری است زیرا خواص قطعه ای را که پس از پخت تشکیل می شود بهبود می بخشند. تعدادی از فرایند های ثانویه در ادامه آمده است:
الف- آهنگری
آهنگری یکی از عملیات ثانویه مهم است که در PM انجام می شود. اگر قطعه ای که طراحی می شود به عنوان اجزا موتورهای جت یا توربین استفاده شود، آهنگری روی قطعات زینتر شده انجام می شود. هدف اصلی آهنگری دستیابی به تلرانس های ابعادی بهتر است. جدای از این تلرانس های ابعادی بهتر، سطح جذاب و مناسبی با آهنگری به دست می آید. اگر می خواهید قطعات در شرایط تنش بالا باقی بمانند، فورج برای شما ضروری است.
ب- نفوذ
در فرآیند نفوذ، منافذ قطعات متخلخل با کمک ماده ای که نقطه ذوب بسیار پایینی دارد پر می شود. به دلیل نفوذپذیری، استحکام و همچنین سختی قطعه زینتر شده افزایش می یابد. برای نفوذ آهن از فلزاتی مانند مس استفاده می شود. همراه با استحکام و سختی، چگالی قطعه زینتر شده نیز با کمک نفوذ افزایش می یابد. خواص اضافی قطعات متخلخل با در آغشته سازی قسمت زینتر شده برای مدتی در روغن یا گریس بهبود می یابد تا نتایج لازم حاصل شود. به عنوان مثال، یاتاقان سینتر شده با قرار دادن در روغن گرم شده با 30 درصد حجم خود آغشته می شود.
ج- اتمام
پرداخت مهم ترین جنبه در شکل گیری هر محصول است، تمام تکنیک های تکمیلی برای قطعات زینتر شده نیز اعمال می شود.
این فرآیندهای تکمیل عبارتند از: آبکاری، براق کردن، رنگ آمیزی، پوشش و غیره
1- آبکاری
قطعات زینتر شده به روش آبکاری پوشش داده می شوند. در قطعات متخلخل ممکن است فرآیند خوردگی رخ دهد که منجر به تخریب آنها شود. بنابراین، برای جلوگیری از برهمکنش قطعه متخلخل و با گازهای جوی، آنها توسط فلزات مختلف پوشش داده می شوند. در آبکاری می توانید از مس، نیکل، روی، کروم و همچنین کادمیوم برای روکش کردن قطعات زینتر شده استفاده کنید.
2- رنگآمیزی
رنگ آمیزی به ویژه در مورد قطعات متخلخل آهن انجام می شود. از آنجایی که آهن می تواند به راحتی خورده شود، رنگ آمیزی آن بسیار ضروری است. قطعات آهنی رنگ شده و یا سیاه شده در حمام نمک از خوردگی در امان می مانند.
3- عملیات حرارتی
شکست در فرآیند PM منجر به عدم سختی قطعات متخلخل می شود. و بهترین راه برای سختتر کردن قطعات زینتر شده، گرم کردن آنها است. عملیات حرارتی مرسوم ترین روش سخت شدن است و در متالورژی پودر کاربرد زیادی دارد.
مزایا و معایب متالورژی پودر
در صنعت امروز تولید با کیفیت بالا، کارایی خوب و عدم نیاز به ماشین کاری بسیار مهم است. تکنیک متالورژی پودر در کنار مزایای بسیار، معایبی نیز دارد. با وجود این، متالورژی پودر یک روش تولیدی است که به دلیل مزایای آن اغلب استفاده می شود آما در کنار آن کمبودهایی نیز وجود دارد. قالب های مورد استفاده در متالورژی پودر بسیار پرهزینه است، بنابراین اگر از این روش در تولید انبوه استفاده نشود از نظر اقتصادی ناخوشایند است. اگرچه در این مقاله به مزایا و معایب متالورژی پودر پرداخته می شود، اما مزایای آن بیشتر مورد توجه قرار خواهد گرفت.
مزایای متالورژی پودر:
- با به حداقل رساندن یا حذف تراشه، ضایعات قراضه کاهش می یابد.
- محصول نهایی با دقت بالا و کیفیت سطح مطلوب قابل تولید است.
- متالورژی پودر توانایی کاهش یا حتی از بین بردن فرایندهای اعمال شده در ساخت های متداول را دارد.
- امکان تولید ترکیبات آلیاژهای بسیار مخلوط را فراهم می کند که با متالورژی پودر غیرممکن محسوب نمی شوند ولی با روش های دیگر تولید نمی شوند.
- تولید مواد با نقطه ذوب بسیار بالا را امکان پذیر می کند ، تولید آنها با ریخته گری بسیار دشوار است و بسیار شکننده هستند.
- در قطعات پخته شده ، می توان محصولی تولید کرد که به سطح کاملا پر و تخلخل رسیده باشد و ممکن است دارای ویژگی های روغن کاری خود باشد.
- می توان با ایجاد قالب در متالورژی پودر فرصت تولید انبوه را فراهم کرد، این از نظر تهیه اقتصادی و تولید سریع یک مزیت مهم است.
معایب متالورژی پودر:
- قالب ها می توانند محدود کننده پودرهای فلزی باشند، بنابراین ممکن است محدودیتی برای شکل قطعه ای که تولید می شود، ایجاد شود.
- ممکن است تراکم قطعات پیچیده در محصولاتی که به روش متالورژی پودر تولید می شوند، به صورت همگن توزیع نشود، بنابراین ممکن است این شرایط برای تولید قطعات پیچیده محدود باشد.
- بدون تولید انبوه ، ممکن است از نظر اقتصادی سودمند نباشد زیرا قالبهای مورد استفاده در متالورژی پودر هزینه های بالایی دارند. تولید یک محصول واحد یا تعداد کم باعث افزایش هزینه ها می شود.
- ممکن است برای بهبود خواص قطعات ساخته شده ، مراحل ثانویه طی شود.
- محصولات تولید شده با متالورژی پودر تلرانس زبری بیشتری نسبت به سایر روش ها دارند.
کاربرد های متالورژی پودر
بسیاری از صنایع به دلیل مزایا، سهولت و پایداری، از این روش در تولید استفاده کرده اند:
- هوافضا
- محافظت در برابر سایش
- سلول سوختی
- پردازش مواد
- الکترونیک، مانند مایکروویو RF
ساخت پودر فلز
پودرهای فلزی مواد بسیار ریز تهیه شده ای هستند که معمولاً در روش های تولید استفاده می شوند. به عنوان مثال، برخی از انواع فلزات متداول شامل آهن، آلومینیوم، کبالت، تنگستن، مس، برنز، کاربید فلز و غیره هستند.
پودر فلزات پس از انجام برخی فرآیندها در متالورژی پودر استفاده می شود. اولین مرحله در فرآیند متالورژی پودر با تولید فلز پودر آغاز می شود. روش های مختلفی برای تولید فلز پودر وجود دارد.
در این روش تولید پودر نقش مهمی ایفا می کند زیرا بدون تشکیل پودر نمی توان این فرآیند را ادامه داد. هنگام تولید پودر از هر ماده ای، اندازه پودر مورد نیاز مهمترین چیزی است که باید به آن توجه کرد. خرد کردن، آسیاب کردن و گاه حتی رسوب الکترولیتی فرآیندهایی هستند که در تولید پودر استفاده می شوند.
پودرهای فلزی در اشکال و اندازه های مختلف وجود دارند. شکل، اندازه و توزیع اندازه آنها به نحوه تولید آنها بستگی دارد.
سه روش اصلی برای تولید پودر وجود دارد:
- مکانیکی: از جمله ماشینکاری، فرزکاری و آلیاژسازی مکانیکی
- شیمیایی: از جمله رسوب الکترولیتی، تجزیه جامد توسط گاز، تجزیه حرارتی، رسوب از مایع، رسوب از گاز، سنتز واکنشی جامد-جامد
- فیزیکی: از جمله تکنیک های اتمیزه کردن بیشتر فلزات به شکل پودر در دسترس هستند.
برخی ممکن است با روش های مختلف ساخته شوند، در حالی که برای برخی دیگر تنها چند گزینه ممکن است. ویژگی های پودر با روشی که توسط آن تولید می شود تعیین می شود. شکل، اندازه، توزیع اندازه، مساحت سطح، چگالی ظاهری، جریان، زاویه قرارگیری، تراکم پذیری و مقاومت خام به روش تولید پودر بستگی دارد.
تکنیک های تولید پودر
1- اتمیزه کردن
متداول ترین روش برای تولید پودر از مواد، اتمیزه کردن است. در اتمیزه کردن، ماده از حالت جامد به حالت مذاب تبدیل می شود. سپس حالت مذاب فلز تحت فشار زیاد از داخل سوراخی عبور داده می شود. هنگامی که این ماده مذاب با فشار زیاد از دهانه عبور می کند، تلاطمی ایجاد می شود که به نوبه خود منجر به تشکیل پودر و ذرات گاز می شود. بعداً ذرات گاز و پودر از هم جدا می شوند.
آیا می دانید که سه نوع فرآیند اصلی اتمیزه شدن وجود دارد؟
این سه عبارتند از: اتمیزه کردن مایع، اتمیزه کردن گاز، اتمیزه کردن گریز از مرکز. تنها نقطه ضعف فرآیند اتمیزه کردن این است که گاهی اوقات عبور دادن مواد مذاب خاص از ساختارهای روزنه ای بسیار دشوار است. در چنین مواردی، اندازه پودر حاصل محدود می شود.
در روش اتمیزه، فلز مذاب با افشاندن به قطرات ریز تبدیل می شود، انجماد قبل از برخورد با یکدیگر یا سطح جامد انجام می شود. عمدتا، فلز مذاب با استفاده از گازهای پر انرژی یا جت های مایع تجزیه می شود. مهمترین نمونه های این روش می تواند قلع، برنج، مس، آلومینیوم، کادمیوم، روی باشد.
در مورد روش های تولید پودر اتمایز بیشتر بخوانید
2- فرآیند آهن اسفنجی
از فرآیند آهن اسفنجی به عنوان پرکاربردترین روش تولید پودر پس از اتمیزه کردن یاد می شود. در این فرآیند، پودر با کمک احیای حالت جامد تولید می شود. اول از همه، اختلاط سنگ معدن مگنتیت با آهک و همچنین کک صورت می گیرد و کل این مخلوط در مخزن کاربید سیلیکون قرار داده می شود سپس مجدداً حرارت داده شده و متعاقباً مخلوط موجود در مخزن کاهش می یابد(احیا می شود) که به نوبه خود منجر به تشکیل سرباره می شود. در مرحله آخر، کل مخزن تخلیه شده و آهن اسفنجی که در قالب احیا شده است از سرباره تشکیل شده جدا می شود. خرد کردن و همچنین بازپخت شدن آهن اسفنجی برای تشکیل پودر ماده صورت می گیرد.
اگرچه این یکی از پرکاربردترین روش های تولید پودر است، اما دارای معایبی است. فرآیند آهن اسفنجی منجر به تشکیل پودری می شود که حاوی دانه های کوچک با شکل غیر یکنواخت است. بنابراین، چنین دانههایی با شکل غیریکنواخت میتوانند منجر به نقص در کل فرآیند شوند.
3- تجزیه ذرات با گریز از مرکز
تجزیه گریز از مرکز یکی دیگر از روش های رایج برای تهیه پودر از فلز است. فلزی که باید پودر شود ابتدا به ساختار میله ای تبدیل می شود. سپس این میله در محفظه ای قرار می گیرد که شامل یک دوک است که با سرعت بالایی می چرخد. از آنجایی که این دوک دارای دو نوک است، از یک نوک این دوک برای ایجاد قوس لازم استفاده می شود که میله را ذوب می کند. از آنجایی که دوک با سرعت بالا در حال چرخش است، قطرات مذاب میله را به دیواره های محفظه پرتاب می کند. اما قبل از برخورد به دیوارها، این قطرات به شکل جامد در می آیند. سپس گاز به گردش در می آید که کار جداسازی پودر را از محفظه انجام می دهد.
از آنجا که پودر فلزات خصوصیات مختلفی دارند، برای روشهای تولید متالورژی پودر انواع مختلف طبقه بندی وجود دارد. نوع دیگری از طبقه بندی تولید پودر به چهار روش احیا حالت جامد، اتمیزه(اتمایزه کردن)، الکترولیز و روش شیمیایی تقسیم شده است.
الف- احیا حالت جامد
روش احیا حالت جامد روشی است که به طور مکرر در تولید پودر استفاده می شود. در روشی که از اسفنج آهنی تشکیل شده و در انتهای آن الک می شود ، مواد اولیه عبوری از درون کوره، خرد شده و با کربن مخلوط می شود و یک واکنش ایجاد می شود. خلوص گرد و غبار تشکیل شده به کیفیت ماده اولیه بستگی دارد. ذرات شبیه اسفنج نامنظم، نرم و به راحتی فشرده میشوند که می تواند به خوبی پخته شود.
ب- الکترولیز
در ترکیب الکترولیتی ساخته شده با اعمال شرایطی مانند دما و چگالی جریان، بسیاری از فلزات مانند اسفنج یا به صورت پودر تشکیل می شوند. فرایندهایی مانند خشک کردن، شستشو، احیا، خرد کردن را می توان اعمال کرد و در نتیجه ، پودرهای با چگالی بالا و خلوص بالا تشکیل می شوند. مس مهمترین نمونه تولید شده توسط این روش است. پودرهای آهن، منیزیم و کروم نیز نمونه هایی از پودرهای تولید شده توسط این روش هستند.
ج- شیمیایی
روش شیمیایی یکی از پرکاربردترین روشهای تولید فلز پودر است ، در این روش احیای اکسید، رسوب و تجزیه اساسی است. این فرآیند اولین بار با تصفیه نیکل آغاز شد. پودرهای کاهش یافته (احیا شده) اکسید به دلیل داشتن منافذ، ساختاری اسفنجی دارند. پودرهای رسوبی ذرات باریک با خلوص بالایی دارند. از تجزیه حرارتی اغلب برای کربونیل ها استفاده می شود. در نتیجه این فرآیند می توان به خلوص 95.5٪ دست یافت.
کاربردهای متالورژی پودر در صنعت خودرو
صنعت خودرو یکی از مهمترین بخشهای صنعتی در جهان است. متالورژی پودر سهم زیادی در صنعت خودرو و همچنین در بسیاری از بخشهای صنعتی در جهان دارد. تولید با متالورژی پودر در مقایسه با روشهای ریخته گری و ساخت متداول، کاربردی تر است. به طور کلی، قطعاتی که تولید آنها با ریخته گری و روش های ساخت کلاسیک دشوار یا غیرممکن است، می توانند توسط متالورژی پودر تولید شوند. اتومبیل های اروپایی شامل 7 کیلوگرم ، ماشین های ژاپنی 5 کیلوگرم، اتومبیل های آمریکایی حاوی بیش از 16 کیلوگرم متالورژی پودر هستند.
قطعات تولید شده توسط متالورژی پودر در اتومبیل، موتور، شاسی، سیستم انتقال قدرت و سایر قطعات است. قطعات قابل تولید با متالورژی پودر در خودروها در شکل نشان داده شده است.
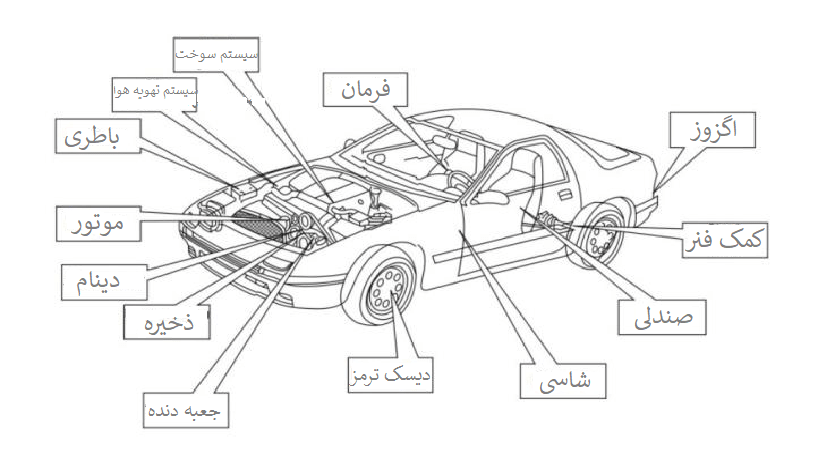
فیلمی کوتاه از نحوه متالورژی پودر:
منابع:
https://www.mechanicalbooster.com