ceramic محصولی از دوغاب است که به صورت خمیر در می آید و در کوره پخته می شود. در نتیجه، محصولی با خواص عالی ایجاد می شود. مواد سرامیکی دارای خواص مکانیکی مناسب و هدایت حرارتی پایینی هستند. بنابراین از آنها در کاربردهای نسوز و پوشش دهی استفاده می شود. پودرهای سرامیکی نانو نیز به دلیل اندازه بسیار کوچک از اهمیت بالایی در صنعت برخوردار هستند. نانوسرامیک ها به مواد سرامیکی اطلاق می شود که از ذرات بسیار ریز با قطر کمتر از 100 نانومتر ساخته شده و به عنوان جامدات غیرآلی، مقاوم در برابر حرارت و غیرفلزی طبقه بندی می شوند.
ذرات نانوسرامیک را می توان برای ترمیم استخوان، دارورسانی، تامین و ذخیره انرژی، ارتباطات، سیستم های حمل و نقل، پوشش دهی و ساخت قطعات، عایق حرارتی، عایق الکتریکی و … استفاده کرد. پودر نانو سرامیک بازار رو به رشدی دارد پودر نانو سرامیک مقاومت بالایی داشته و استحکام این پودرها مشابه فولاد است.
پودر نانو سرامیک چیست؟ اکسیدهای فلزی ساده، سیلیس (SiO2)، تیتانیا (TiO2)، آلومینا (Al2O3)، اکسید آهن (Fe3O4، Fe2O3)، اکسید روی (ZnO)، سریا (CeO2) و زیرکونیا (ZrO2) نمونه های رایج نانوسرامیک های تجاری مهم هستند. همانطور که گفتیم، پودرهای نانو کاربردهای متنوعی دارند. به عنوان مثال، از ترکیبات سرامیکی اکسید زیرکونیوم برای کاربردهای با درجه حرارت بالا استفاده می شود. علاوه بر کاربردهای دمای بالا، از پودرهای سرامیکی در پوشش ها نیز استفاده می شود.
به عنوان مثال، پوشش های نانو اکسید آلومینیوم مقاومت در برابر سایش را افزایش می دهند. با این وجود هزینه تولید پودر سرامیک نانو گران است. بنابراین، محققان به دنبال راه هایی برای تولید پودر سرامیک نانو به روشی ارزان تر هستند. به دلیل اندازه و ساختار مولکولی، پودرهای نانو خواص ویژه ای دارند. از ویژگی های اصلی پودر نانو سرامیک می توان به مقاومت در برابر سایش، مقاومت در برابر خوردگی اشاره کرد.
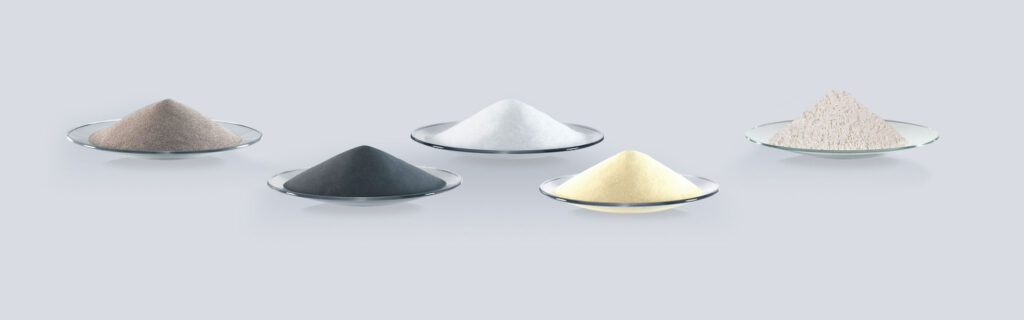
روش های تولید نانو ذرات سرامیکی
روشهای مختلفی برای تولید پودرهای نانو وجود دارد، نانوسرامیکها ابتدا با استفاده از فرآیند سل-ژل – شکلی از رسوبگذاری محلول شیمیایی – که نانوذرات را در محلول و ژل مخلوط میکند و نانوسرامیکها را تشکیل میدهد، شکل گرفتند. در دهه 2000 روش های تولید شروع به استفاده از گرما و فشار در فرآیند تف جوشی کردند..
آسیاب گلوله ای
متداول ترین روش تولید پودر نانو روش آسیاب با گلوله می باشد. در واقع در روش Ballmilling ذرات پودر با ساییدگی های مکانیکی متعدد خرد شده و به اندازه نانو تبدیل می شوند. آسیاب گلوله ای فرآیند خرد کردن و مخلوط کردن مواد با یکدیگر است. علاوه بر تولید پودر نانو سرامیک، از این روش می توان برای مخلوط کردن پودرها نیز استفاده کرد. در این روش از توپ هایی (توپ های آلومینا یا زیرکونیا) استفاده می شود که در داخل ویال گردش می کنند. با هر حرارتی که گلوله ها به پودر وارد می کنند، اندازه پودر کاهش می یابد. پودرهای سرامیکی مخلوط، ناشی از Ballmilling، باید پخته شوند. برای این منظور از کوره های با درجه حرارت بالا استفاده می شود.
مزایا و معایب تولید پودر سرامیک نانو توسط Ballmilling
مزایا
- ارزان
- فرآیند در مقیاس بزرگ
- فرآیند کاملاً تثبیت شده قدیمی
- ممکن است به 2 تا 20 نانومتر برسد
معایب
- نانوذرات نامنظم
- ایجاد نقص
- ایجاد ناخالصی های حاصل از گلوله ها و مواد افزودنی فرز
روش های شکل دهی ذرات سرامیکی
برای تولید قطعات سرامیکی روش های مختلفی وجود دارد که تعدادی از آنها در ادامه ذکر شده است. پودرهای سرامیکی با خرد کردن یا آسیاب کردن (به دنبال الک کردن) ساخته می شوند – ذرات بسیار نامنظم هستند. شکل ذرات مهم است زیرا: ذرات نامنظم به خوبی به هم «کلید» میشوند و بنابراین وقتی به هم فشرده میشوند تمایل دارند به هم بچسبند که منجر به اجزای سبز قویتر از ذرات گرد میشود.
فشرده سازی
از این روش برای تبدیل پودر سرامیک از حالت دانه ای به فرم منسجم تر و متراکم تر استفاده می شود. همانطور که از نام آن پیداست، این فرآیند پودر سرامیک را فشرده تر می کند. تراکم پودرهای سرامیکی را می توان از طریق پرس گرم یا پرس سرد انجام داد. محصول این فرآیند معمولاً ماده سبز نامیده می شود. این ماده سبز وارد مرحله پخت میشود. پس از فرآیند تراکم، مواد باید عاری از نقص بزرگ و امکان مانور باشد.
قالب گیری تزریقی
از قالب گیری تزریقی برای تولید مواد سرامیکی با هندسه پیچیده استفاده می شود. از این فرآیند می توان برای تولید مواد سرامیکی در مقادیر زیاد استفاده کرد. قالب گیری تزریقی یک فرآیند همه کاره است. هم برای سرامیک های اکسیدی و هم برای سرامیک های غیر اکسیدی استفاده می شود. علاوه بر این، دقت بالایی دارد. محصول نهایی قالب گیری تزریقی از کیفیت بالایی برخوردار است. پودر سرامیک با چسب پلیمری مخلوط شده و در این فرآیند حرارت داده می شود. قالب گیری تزریقی مواد را جمع می کند. با این حال، انقباض در طول فرآیند پخت جبران می شود.
ریخته گری نواری
ریخته گری نواری یکی دیگر از روش های رایج تولید پودرهای سرامیکی است. در ساخت بسترهای مدارهای چاپی و خازن های چندلایه کاربرد دارد. یک پودر سرامیکی مخلوط با یک حلال آلی و چسب پلیمری به طور مکرر بر روی یک سطح حامل ریخته می شود. سطح حامل از ماده ای مانند تفلون ساخته شده است که نچسب است. سپس مخلوط پودر سرامیک (دوغاب) با استفاده از لبه تیز ورقه ای چاقو مانند به ضخامت مشخصی روی سطح صاف پخش می شود. لایه مخلوط پودر سرامیک خشک می شود و برای پردازش بیشتر آماده است.
ریخته گری ژل
ریخته گری ژل روشی برای تولید پودرهای سرامیکی است که در دهه 1960 در کانادا آغاز شد. برای تولید اشکال پیچیده سرامیکی با کیفیت و استحکام بالا استفاده می شود. در این روش پودر سرامیک با یک مونومر، پیوند متقاطع و آغازگر رادیکال آزاد مخلوط می شود. سپس مخلوط به یک سوسپانسیون آبی اضافه میشود. چسب موجود در مخلوط پلیمریزه می شود تا سفتی بیشتر به مخلوط اضافه شود. در نتیجه مخلوط به شکل ژل در می آید. مخلوط ژل در قالب ریخته می شود و در آنجا جامد می شود. پس از سفت شدن مخلوط، آن را از قالب خارج کرده و خشک می کنند. محصول نهایی یک بدنه سبز (خام)است که متعاقباً پخته می شود.
اکستروژن
اکستروژن یک روش تولید پودر سرامیک است که می توان از آن برای شکل دادن سرامیک ها به شکل استفاده کرد. پودر سرامیک از طریق یک قالب با سطح مقطع مشخص کشیده می شود. از این روش می توان برای ساخت سرامیک هایی با مقاطع پیچیده استفاده کرد. علاوه بر این، مواد را تحت فشار کافی قرار نمی دهد تا آنها را بشکند. محصولات نهایی حاصل از این فرآیند دارای سطح نسبتا صاف و استحکام بالایی هستند. اولین فرآیند اکستروژن در سال 1797 انجام شد. این فرآیند توسط فردی به نام جوزف براما انجام شد. اکستروژن ممکن است گرم یا سرد باشد. اکستروژن داغ در دمایی رخ می دهد که از دمای تبلور مجدد ماده بیشتر باشد. اکستروژن سرد در دمای اتاق اتفاق می افتد در حالی که اکستروژن گرم بالاتر از دمای اتاق و زیر دمای تبلور مجدد ماده رخ می دهد.
تولید کنندگان پودر سرامیک نانو
بیشتر تولید کنندگان پودر سرامیک نانو در سراسر جهان چینی هستند. به عنوان مثال لیانیونگانگ و KINGDA به ترتیب تولید کنندگان عمده اکسید آلومینیوم و زیرکونیوم هستند.