سختی مقاومت مواد در برابر تغییر شکل موضعی است. سختی را باید در چارچوب سایر خواص مواد مانند استحکام، کشش، کشسانی (الاستیسیته) و غیره مشاهده کرد. به عنوان مثال، بسیاری از مواد سخت شکننده هستند و این موارد استفاده از آنها را محدود میکند. در این مقاله، نگاه دقیق تری خواهیم داشت به اینکه سختی ماده چیست، چگونه اندازه گیری می شود و چگونه واحدهای مختلف را با هم مقایسه می کنیم.
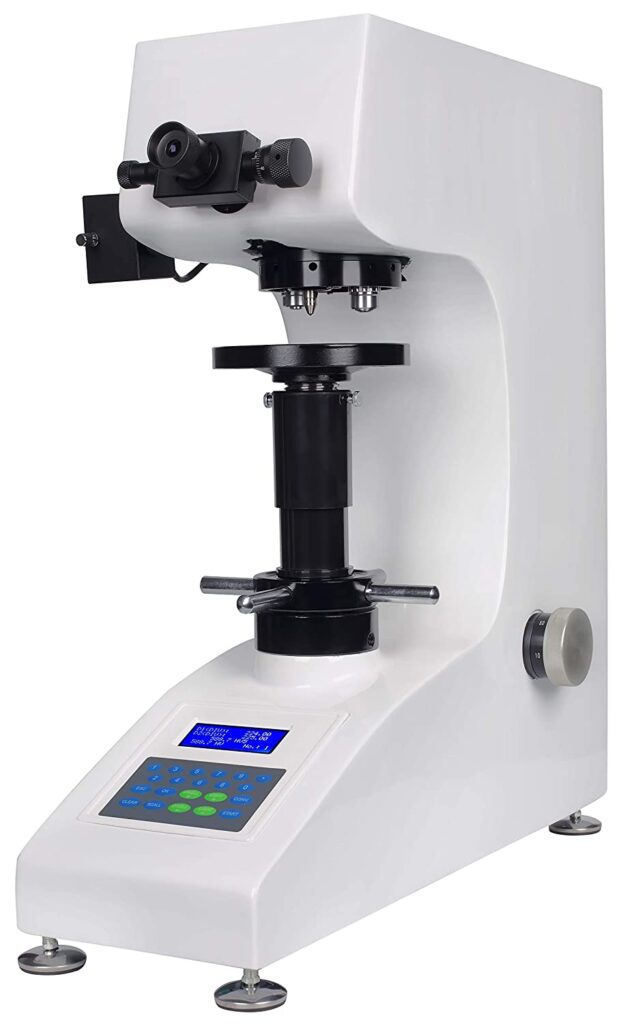
سختی مواد چیست؟
سختی اندازه گیری مقاومت یک ماده در برابر تغییر شکل دائمی موضعی است. تغییر شکل دائمی را تغییر شکل پلاستیک نیز می نامند. در حالی که تغییر شکل الاستیک به این معنی است که ماده فقط در هنگام اعمال نیرو شکل خود را تغییر می دهد، تغییر شکل پلاستیکی حاصل به این معنی است که ماده به شکل اولیه خود برنخواهد گشت.
بعضی از مواد به طور طبیعی سخت هستند. به عنوان مثال، تنگستن یک فلز فوق العاده سخت است که به عنوان یک عنصر آلیاژی در فولادهای ابزار استفاده می شود. که این گروه از فولادها حتی در دمای بالا در حین عملیات برش می توانند در برابر سایش مقاومت کنند.
تنگستن یکی از اجزای Cemented carbide هاست که کاربرد زیادی در فرزها دارد. این مته های ابزار برش قابل تعویض، به طور قابل توجهی طول عمر ابزارهای برش را افزایش می دهند.
از طرف دیگر ، برخی از مواد ، از جمله فلزات ، تا حدی نرم هستند که آنها را برای بسیاری از کاربردها بی فایده می کند. طلای خالص به قدری نرم است که خراشیدن یا خم شدن آن نیاز به تلاش زیادی ندارد. بنابراین افزودن فلزات دیگر مانند نقره ، مس و آلومینیوم برای بهبود سختی آن ضروری است.
انواع سختی
مواد تحت انواع مختلف بارگیری رفتار متفاوتی دارند. به عنوان مثال، فلزی که می تواند یکبار مقاومت به ضربه بزرگی ایجاد کند، ممکن است تحت بارگذاری مداوم عمل نکند.
سه نوع سختی وجودارد: سختی خراش، سختی برگشت پدیر و سختی فرورونده. اندازه گیری هر نوع سختی به مجموعه متفاوتی از ابزار نیاز دارد. همچنین، همان ماده برای هر یک از انواع فوق الذکر مقادیر سختی متفاوتی خواهد داشت.
سختی فرورونده
این نوع سختی به مقاومت در برابر تغییر شکل دائمی هنگام قرار دادن ماده در معرض بار پیوسته اشاره دارد. سختی فرورونده همان چیزی است که مهندسان و متالورژیست ها هنگام صحبت در مورد سختی معمولاً به آن اشاره می کنند. اندازه گیری مقدار آن از اهمیت اولیه برخوردار است زیرا بارگذاری مداوم متداول ترین شکل بارگذاری فلزات است.
سختی خراش
این نوع سختی به توانایی ماده در مقاومت در برابر خراش های سطح اشاره دارد. خراش ها به دلیل تماس با ماده ای تیز و سخت تر، فرورفتگی های باریک و مداوم در لایه فوقانی هستند. آزمایش خراش همچنین معمولاً برای مواد شکننده مانند سرامیک استفاده می شود زیرا تغییر شکل قابل توجهی در پلاستیک ندارند. آستر سیلندر موتور را به عنوان مثال در نظر بگیرید. خراشیدن به دلایل مختلفی انجام می شود. سطح بوش با انواع فلزات مانند حلقه های پیستون ، ذرات خارجی موجود در سوخت یا روغن روانکاری در تماس است. بعضی اوقات نشستن نامناسب آستر می تواند به آن کمک کند.
ذرات ساینده می توانند باعث ایجاد خراش هایی شوند که در نهایت باعث کاهش عملکرد موتور شده و در طولانی مدت هزینه های بیشتری را برای تعمیر و نگهداری، قطعات یدکی و مصرف سوخت دارند.سختی آستر باید بیشتر از موادی باشد که با آن تعامل خواهد داشت. این به جلوگیری از بسیاری از مسائل احتمالی کمک می کند.
سختی برگشتی یا دینامیکی
سختی برگشتی بیشتر از سختی پلاستیکی به سختی الاستیک مربوط است. این ماده انرژی را در اثر ضربه جذب می کند و آن را به داخل فرورفتگی برمی گرداند.
فرو رفتگی ماده مرجعی است که برای آزمایش سختی استفاده می شود. سختی دینامیکی معمولاً با انداختن فرورونده نوک الماس بر روی قطعه آزمایش و جهش فرورونده پس از برخورد به سطح، اندازه گیری می شود. هرچه ارتفاع به ارتفاع اولیه نزدیکتر باشد ، مقدار سختی برگشت نیز بیشتر است.
واحدهای مختلف سختی
واحد سختی SI برابر N / mm² است. بنابراین واحد Pascal برای سختی نیز استفاده می شود اما سختی را نباید با فشار اشتباه گرفت.
انواع مختلف سختی مورد بحث در مقیاس های مختلفی اندازه گیری می شوند. برای خراش، فرورفتگی و سختی برگشت، روشهای اندازه گیری متفاوت است (به عنوان مثال برینل ، راکول ، نوپ ، لیب و میر). از آنجا که واحدها از این روش های اندازه گیری گرفته شده اند، برای مقایسه مستقیم مناسب نیستند.
با این حال، همیشه می توانید از جدول تبدیل برای مقایسه مقادیر Rockwell (B & C)، ویکرز و برینل استفاده کنید. جداولي از اين قبيل 100٪ دقيق نيستند اما نشانگر خوبي هستند.
Brinell Hardness | Rockwell | Rockwell | Vickers | N/mm² |
HB | HRC | HRB | HV | |
469 | 50 | 117 | 505 | |
468 | 49 | 117 | 497 | |
456 | 48 | 116 | 490 | 1569 |
445 | 47 | 115 | 474 | 1520 |
430 | 46 | 115 | 458 | 1471 |
419 | 45 | 114 | 448 | 1447 |
415 | 44 | 114 | 438 | 1422 |
402 | 43 | 114 | 424 | 1390 |
388 | 42 | 113 | 406 | 1363 |
375 | 41 | 112 | 393 | 1314 |
373 | 40 | 111 | 388 | 1265 |
360 | 39 | 111 | 376 | 1236 |
348 | 38 | 110 | 361 | 1187 |
341 | 37 | 109 | 351 | 1157 |
331 | 36 | 109 | 342 | 1118 |
322 | 35 | 108 | 332 | 1089 |
314 | 34 | 108 | 320 | 1049 |
308 | 33 | 107 | 311 | 1035 |
300 | 32 | 107 | 303 | 1020 |
290 | 31 | 106 | 292 | 990 |
277 | 30 | 105 | 285 | 971 |
271 | 29 | 104 | 277 | 941 |
264 | 28 | 103 | 271 | 892 |
262 | 27 | 103 | 262 | 880 |
255 | 26 | 102 | 258 | 870 |
250 | 25 | 101 | 255 | 853 |
245 | 24 | 100 | 252 | 838 |
240 | 23 | 100 | 247 | 824 |
233 | 22 | 99 | 241 | 794 |
229 | 21 | 98 | 235 | 775 |
223 | 20 | 97 | 227 | 755 |
216 | 19 | 96 | 222 | 716 |
212 | 18 | 95 | 218 | 706 |
208 | 17 | 95 | 210 | 696 |
203 | 16 | 94 | 201 | 680 |
199 | 15 | 93 | 199 | 667 |
191 | 14 | 92 | 197 | 657 |
190 | 13 | 92 | 186 | 648 |
186 | 12 | 91 | 184 | 637 |
183 | 11 | 90 | 183 | 617 |
180 | 10 | 89 | 180 | 608 |
175 | 9 | 88 | 178 | 685 |
170 | 7 | 87 | 175 | 559 |
167 | 6 | 86 | 172 | 555 |
166 | 5 | 86 | 168 | 549 |
163 | 4 | 85 | 162 | 539 |
160 | 3 | 84 | 160 | 535 |
156 | 2 | 83 | 158 | 530 |
154 | 1 | 82 | 152 | 515 |
149 | 81 | 149 | 500 |
در تمام این مقیاس ها، یک ماده سخت عدد سختی بیشتری خواهد داشت.
واحدهای متداول اندازه گیری سختی عبارتند از:
- عدد سختی برینل (HB)
- عدد سختی ویکرز (HV)
- عدد سختی راکول (HRA ، HRB ، HRC و غیره)
- مقدار سختی Leeb (HLD ، HLS ، HLE و غیره)
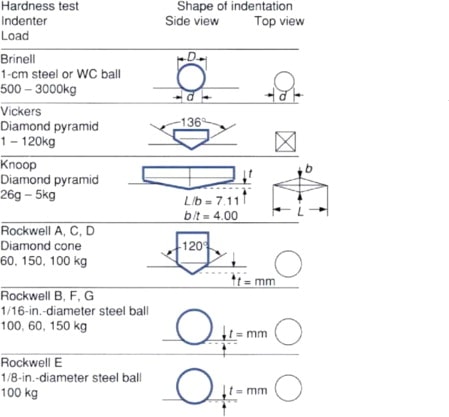
اندازه گیری سختی
انواع مختلف سختی با استفاده از روش های آزمایش مختلف اندازه گیری می شود. یک وجه مشترک در بین همه روش ها استفاده از فرورونده برای ایجاد فرورفتگی در سطح آزمایش است. فرورفتگی نمایشی ملموس از سختی مواد را فراهم میکند و اندازه گیری آن آسان است.
مواد سخت تر دارای فرورفتگی های کم عمق و مواد نرم تر دارای فرورفتگی های عمیق تر خواهند بود.
تست سختی برینل
آزمون برینل یکی از اولین آزمایش های سختی پذیرفته شده برای اندازه گیری سختی فرورونده بود. در آزمایش برینل، از یک گلوله فولادی به قطر 10 میلی متر به عنوان فرورونده استفاده میشود تا بر روی قطعه آزمایش تأثیر بگذارد تا عدد سختی برینل آن محاسبه شود.
گلوله برای مدت زمانی از پیش تعیین شده، معمولاً 30 ثانیه در جای خود نگه داشته می شود و نیرویی روی گلوله وارد میشود. این نیرو بسته به فلز آزمایشی که اندازه گیری می شود متفاوت خواهد بود.
بار استاندارد 3000 کیلوگرم است، اما ممکن است برای فلزات نرمتر به 500 کیلوگرم کاهش یابد. برای فلزات سخت تر، ممکن است از یک گلوله کاربید تنگستن برای جلوگیری از اعوجاج گلوله استفاده شود. واحد سختی HB (یا HBN) در صورت وجود تنگستن به HBW تغییر می یابد تا کاربرد آن را اعلام کند.
با برداشتن فرورونده، فرورفتگی با میکروسکوپ معمولی مشاهده میشود و اندازه گیری آن با میانگین اندازه گیری ها در زاویه درست انجام می شود.
تست سختی راکول
آزمایش سختی راکول متداول ترین روش برای اندازه گیری سختی فرورفتگی است. مقدار سختی Rockwell با مقیاس مورد استفاده همراه است. بسته به ماده مورد آزمایش، مقیاس مناسبی باید انتخاب شود. این مقیاس سختی، اطلاعاتی را در مورد نوع بار فرورفتگی استفاده شده ارائه میدهد.
در کل 30 مقیاس برای انتخاب موجود است. این همان چیزی است که راکول را به یک آزمون معیار برای سنجش سختی آرایه وسیعی از مواد تبدیل می کند. اندازه گیری سختی مواد سرامیکی و کامپوزیت نیز امکان پذیر است. مقیاس های متداول “B” و “C” هستند. در آزمایش سختی راکول، قبل از استفاده از بار آزمایش، بار جزئی برای نشستن فرورونده داخل قطعه آزمایش و از بین بردن اثر هرگونه بی نظمی سطح اعمال می شود.
سپس مشابه آزمایش برینل، از فرورفتگی برای ایجاد تأثیر بر روی مواد با استفاده از بار آزمایش که به عنوان بار اصلی نیز شناخته می شود، استفاده می شود. سپس اثر برای تعیین سختی اندازه گیری می شود. برای ثبت تغییر شکل از یک صفحه سنج استفاده می شود.
برای محاسبه مقدار سختی، افزایش خالص در ابعاد فرورفتگی (بین اعمال بار جزئی و بزرگ) در نظر گرفته شده است.
تعیین سرعت بارگیری ضروری است. در فلزات نرم، سرعتهای مختلف بارگذاری می تواند اختلاف قابل ملاحظه ای در مقدار نهایی ایجاد کند. مهم است که به دقت نظارت کنید که میزان بارگیری مطابق با استاندارد باشد.
تست سختی ویکرز
روش سوم برای اندازه گیری سختی مواد استفاده از تست ویکرز است. این امر مخصوصاً برای مواد نرمتر که به بار زیادی احتیاج ندارند مناسب است. برای استفاده در مواد نرم ، روش ویکرز دقت بهتری را ارائه می دهد.
همچنین، محاسبه مقدار سختی آسان تر است، زیرا ویکرز برای همه مواد از همان تورفتگی الماس استفاده می کند. بنابراین، دستکاری فرمول ضروری نیست.
ویژگی مهم دیگر استفاده از ذره بین است که امکان آزمایش مناطق با ریزساختار خاص را فراهم می کند. ابتدا آزمایش کننده باید قطعه را روی دستگاه قرار داده و از میکروسکوپ برای یافتن ارتفاع مناسب استفاده کند. سپس با استفاده از تصاویر ، مکان صحیح تعیین می شود.
فرورفتگی الماس به شکل یک هرم چهار طرفه است. پس از لمس قطعه، دستگاه به زودی به مقدار نیروی از پیش تعیین شده می رسد. مدت زمان مشخصی در همان بار باقی می ماند.
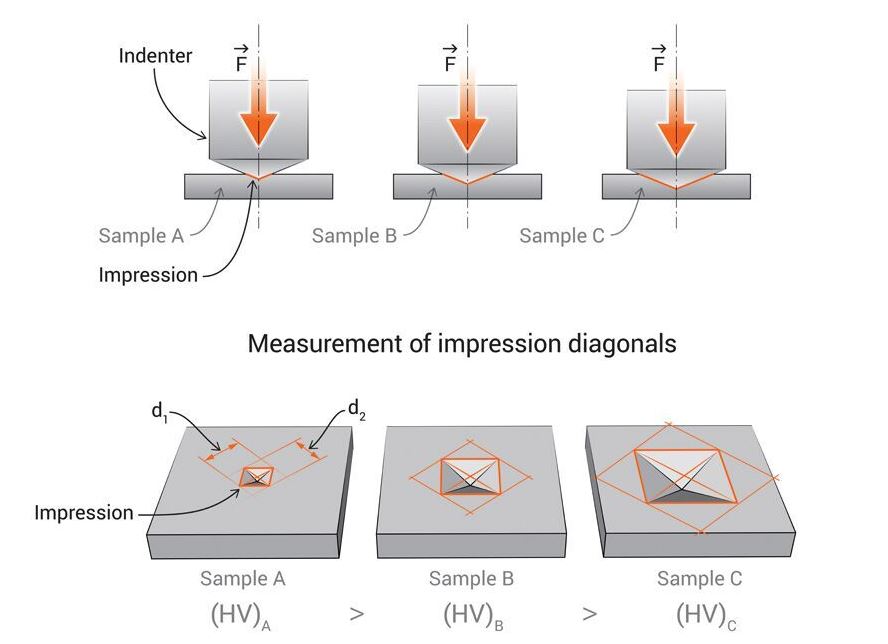
آزمایش سختی Mohs
Mohs متخصص معدنی آلمانی ابتدا آزمایش سختی Mohs را اندازه گیری کرد تا سختی خراش مواد اندازه گیری شود. در این آزمایش، ماده با ماده مرجعی که دارای سختی مشخص است خراشیده می شود. بر اساس نتایج آزمون مقدار سختی عددی به ماده آزمون اختصاص داده می شود. آزمون سختی Mohs از 10 ماده مرجع با سختی متفاوت به عنوان مقیاس آزمون استفاده می کند.
نرم ترین ماده استفاده شده تالک است (مقدار 1 =) و سخت ترین ماده الماس است (مقدار 10 =). با توجه به اینکه منابع مورد استفاده برای مقیاس Mohs افزایش درجه ای ندارند، مقیاس Mohs فاقد دقت است و فقط اندازه گیری تقریبی سختی است.
امروزه آزمایشات خراش مدرن با استفاده از فرورونده الماس Rockwell با خراش دادن قطعه آزمایش برای یک طول خاص که با مقدار بار انتخابی فشرده میشود ، انجام میشود.
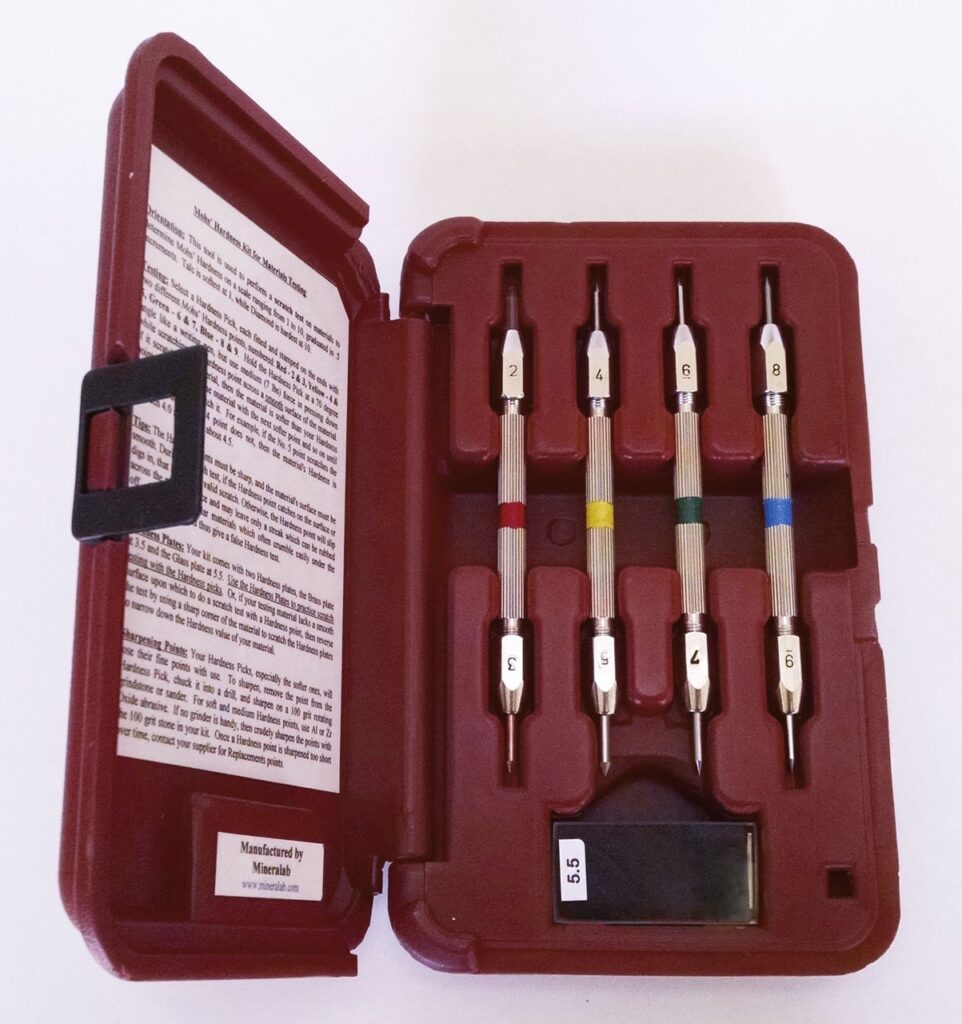
تست اسکلروسکوپ
اسکلروسکوپ دستگاهی است که برای اندازه گیری برگشت یا سختی دینامیکی مواد استفاده می شود. این تنظیم شامل یک لوله شیشه ای عمودی توخالی است که به یک پایه متصل است. از طریق این لوله ، یک فرورونده یا چکش الماس بر روی قطعه آزمایش افتاده و میزان پرش چکش ثبت می شود.چکش الماس از ارتفاع ثابت و تحت وزن خود افتاده است. در تماس با قطعه آزمایش ، چکش برمی گردد. این پرش برای مواد با سختی بالاتر بیشتر خواهد بود.
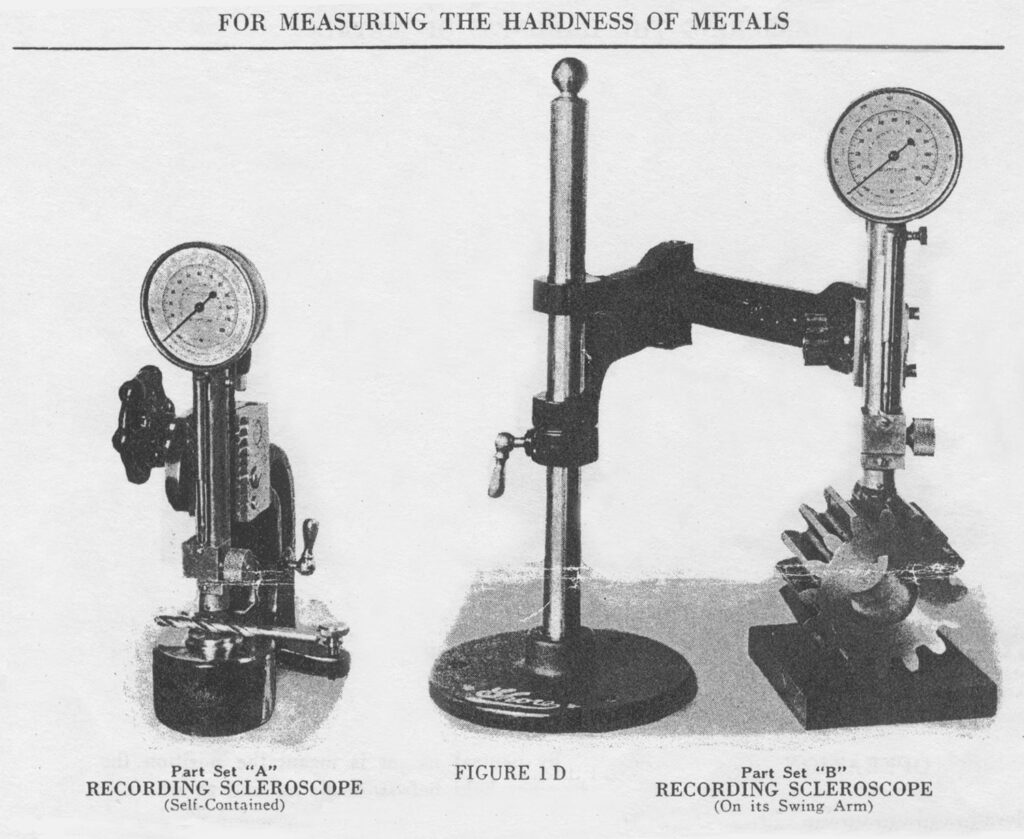
پرش برای یک فلز نرم کمتر خواهد بود زیرا بخشی از انرژی ضربه در ایجاد فرورفتگی روی سطح آزمایش از بین می رود. لوله شیشه ای دارای شیب هایی برای اندازه گیری ارتفاع پرش است. سختی برگشتی در واحدهای ساحلی اندازه گیری می شود.
منابع:
https://fractory.com/material-hardness/